This article is designed to help reduce the learning curve for first-time water jet users. First we must make some assumptions (yes, we know what happens when you assume, but we feel we're on solid ground here) to create this guide.
- Your company has installed and prepared the system for use.
- You operate CAD/CAM software.
- You have designated an operator to train and lead the water jet production.
- All operators have read the water jet’s operating manual and the Safety section contained within it.
Pretty straight-stick stuff, right? Now it's time to start.
Safety First
Water jets are industrial cutting tools operating at high voltage and are capable of inflicting severe injuries in the blink of an eye. Ensure you know how to use your water jet system safely as outlined in the owner’s manual and your company’s safety policies. Here are a few extracts from our upcoming blog on system safety:
- Review the product manuals and highlight the safety information contained in them.
- Read through the operating procedures before operating the equipment and make sure you understand all controls.
- Make sure the work area around the equipment is clean, dry, and clear of any hazards that may cause you to trip or stumble.
- Clear the work area of bystanders and ensure that all personnel not involved with the operation of the equipment are a safe distance from the equipment before cutting starts.
- Locate all emergency stops so the equipment can be quickly shut down in an emergency.
- Make a trial run through the operating procedures before operating the equipment and make sure you understand all controls.
- Confirm you have all the required PPE (personal protective equipment) available and are trained in their proper use.
- Observe all safety practices detailed in your company’s safety manual and use common sense in combination with the safety protocols listed to reduce and eliminate operating risk.
- If you find an issue that you believe creates a safety risk, stop and get clarification from your safety team before proceeding.
Getting Started
Here are some important tips and best practices to getting started.
Follow an Orderly Start-Up and Shut-Down Process
Best operating practices recommend using an orderly start-up process every time you prepare your system. Creating a check list to work from creates consistency between operators and ensures you will not miss any steps. The brand and/or manufacturer of the system you are using may require different or additional steps so adjust these as needed. A helpful checklist should include:
- Check oil and fluid levels in pumping and hydraulic subsystems.
- If using abrasive, ensure the bulk hopper is full and pressurized.
- Confirm the motion systems table is clean and free of debris, fixtures, or any materials not being cut during this operation.
- Confirm there are no obstructions that will impact the movement of the cutting in any direction.
- Confirm there are no obstructions that will impede the UHP whip, or if utilized, the movement of the UHP swing arm that supplies UHP water to the z-axis assembly .
- Inspect the cutting head and ensure you are using the correct orifice and nozzle combination required for the job and ensure there are no signs of damage.
- Power up the pump and verify the water pressure is being received at the motion system via the pressure gauge.
- Add water to the catch tank if it does not reach the bottom of the slats.
- Confirm the air pressure is being delivered via the pneumatic pressure gauge.
- Confirm the hand valve that controls the water flow to the cutting tool is open.
- Power up the controller.
- Check high pressure lines, fittings, and connectors for leak signs or sounds. These include hydraulic, abrasive supply, water, and air supply lines.
- At the end of the cutting cycle clean the table and any areas where splash occurred.
- Shut down your water jet and supporting systems after the production run following the startup process in reverse.
Note: Your operating manual will have a start-up routine that should be followed. Observe the routine and report any unusual or unexpected results before proceeding.
Important: Keep in mind that the time your start-up takes will grow shorter with experience. Be patient, learn the process and the idiosyncrasies of your setup and, above all, never skip steps.
Setting Up Your System for the First Cut
Setting up your water jet cutting system for its first cut involves these steps:
- Locate and load the part's digital file.
- Place the stock on the cutting bed and secure it to the table.
- Confirm pump pressure, abrasive flow and nozzle/orifice combination are per the part requirements.
- Establish the cut's starting point.
- Perform a dry run to validate the program path.
- Make the cut.
- When the gantry has fully stopped, clean the part and retrieve it.
Locating and Loading the Digital File
Usually, the part design that creates the part geometry is done via CAD (computer aided design) software run on a separate IT platform. The CAD files are converted to machine code via a CAM (computer aided manufacturing) process and an .NC part file is created. The resulting .NC part file works with the water jet’s control software to position the cutting tool, regulate the cutting tool height, define feed rates, activate the required pump pressure, and begin the garnet delivery system. The part file may be delivered to the water jet’s controller over the shop’s network or downloaded onto a flash drive and plugged in. Either way, navigate to the proper file and load it into the machine controls. Manual programming or program modifications can be made at the controller unless the operator is locked out and prevented from making changes per process control guidelines.
Ask the engineers to provide a paper copy of the part design that details the raw material being cut, the part number, the part dimensions, and program name. Ideally, set up instructions are included, standard run times estimated and key features details like finish quality are highlighted. The following affects the quality of the finished cut, cutting speed, and the cost of abrasive usage:
- Material being cut
- Type of cut (linear, circular, pierce, etc.)
- Number of cutting tools
- Water volume and pressure
- Orifice and nozzle size
- Feed rate
- Abrasive type and delivery rate
- Cutting head wear
Placement and Securing the Stock
The material being cut must be placed in the cutting envelope defined by the table size of the system and there must be adequate distance from the table sides so no damage is done to the catcher tank. For ease of positioning, the front side closest to the controller is often the preferred placement. The material orientation may not be critical as long as the piece being cut is fully within the blank size.
The water jet cutting operates at high pressure and may cause the material to move if not secured with fixtures or clamps. Large heavy materials may not need to be secured. Smaller, lighter materials may need to be secured so they do not move during cutting or bounce into the catcher tank when the cut is complete. For high precision cutting, fixtures are often designed and integrated into the catcher tank for quick setup and higher process control. When cutting very small parts or parts that may be prone to sagging, water jet bricks may be used.
Best practice: Ensure your part hold down method is defined and does not interfere with the cutting path.
Establishing the Starting Point
Tool movement is accomplished using servomotors, ball screws, ball nuts, and linear bearings in the cross beam, side beams, and z-axis assembly. The cross beam, side beams, and z-axis assembly are assembled together to produce the three planes of movement (x-, y-, and z-axes) of the mid rail 3-axis motion control system. The length of the cross beam and side beams determines the work envelope in which a tool can operate.
The operator needs to establish the X and Y plane “Home” (x=0; y=0) as the cut's starting point, most commonly set at the lower left corner of the stock. To establish home, lower the cutting head to .25" - .5" above the stock surface and jog to the point in which the program is intended to begin. Lower the cutting head to 1/8" from each edge for the fine adjustment of the starting point. Set that current position as home.
A home also needs to be established for the Z-plane (Z=0). To establish home for the nozzle height, utilize a gauge between the stock surface and nozzle tip to ensure the desired standoff distance is achieved. Slide the gauge back and forth under the nozzle while slowly lowering it. You want a snug fit but no resistance to the gauge moving. In other words, you want to feel when the gauge touches the nozzle without impediment. Set that height as the home value.
Best practice: The cut’s starting point is referred to as the lead-in. Beginning the cut in the scrap area of material and "leading-in" to the actual geometry to cut is standard operating procedure in most applications. This avoids placing a blemish from the initial cut. At the end of a cut, a lead-out may be required to remove any "nib" from the lead-in area. Various types of lead-ins and lead-outs can be experimented with for different materials and thicknesses.
Performing a Dry Run
The dry run feature executes the part program axis movement with the cutting heads turned off. The dry run is typically set to run the program as fast as practical. The dry run feature helps validate the program path and will ensure there is no interference from clamps or uneven parts. Raise the cutting head 2" and select the "dry run at full rapid traverse speed" command. Return the head to its correct cutting height following a successful test. Surface detection options like laser mapping or using a height sensor further assists in managing the cutting of non-flat materials. Parameters including feed rates and dwell times can be changed or adjusted based on the results of the dry run.
Making the Cut
Select the program, set the controls to computer control (not manual), ensure the pump is on and delivering the required pressure, the abrasive flow is metered appropriately and then hit run. Note that while running a part program, situations can occur that require you to stop the part program to address a problem. When an issue is detected use the stop cycle switch on the control panel to end the program and then address the issue. In the event of an emergency use the emergency stop to immediately shut down the motion system. The following are some of the reasons for suspending a part program:
- The orifice must be replaced.
- The abrasivejet nozzle has broken and requires replacement.
- The abrasive feed has backed up and requires maintenance.
- The ultra high pressure (UHP) pump has stopped and requires attention.
- A motion control system limit is detected.
- The wrong part program is selected
At the end of the cycle, retrieve your part and rinse it with clear water to remove any garnet residue. Congratulations, you've completed your first cut.
Retrieve the Part
When the cutting has been completed and the motion system has returned to its safe, end point position, it is safe to remove the part. Remove any clamps, wash the part with clean water, inspect the finish quality and part geometry to confirm the first article.
Conclusion
Obviously, this is just a generic high-level overview of water jet cutting with each system having its own unique operating procedures. However, this guide does cover the basics of cutting your first 2D part. It is essential to train your operators in safety and operation before attempting to operate your system. Create and follow a structured start-up/shut-down process each time and always make sure to secure your stock properly. Do these things, and you're well on your way to becoming a master of water jet cutting systems.
Jet Edge Will Help You on the Journey To Water Jet Mastery
Every Jet Edge water jet system includes unlimited lifetime hands-on training. Water jet training is free when taken at Jet Edge’s headquarters. You also can arrange to have training at your facility for a fee. Register for classes online or call 1-800-JET-EDGE to schedule custom training sessions for your business
If you do not have a copy of your Jet Edge Owner’s Manual that outlines the safety protocol and operating procedures, please request one right away from our technical support page. If you would prefer to speak with our Technical Service Team regarding a specific issue please contact a team member.
Visit our Blog Library and Comprehensive Video Collection
Jet Edge offers a comprehensive library of maintenance training videos, case studies, best practice blogs and a whole lot more in our resource center.
If you would like to learn more about Jet Edge Water jet Systems, visit us online at jetedgewaterjets.com. If you are ready to speak with your regional expert, just let us know on our contact us page, or call us toll-free at 1-800-JET-EDGE (538-3343), internationally at +1-763-497-8700.
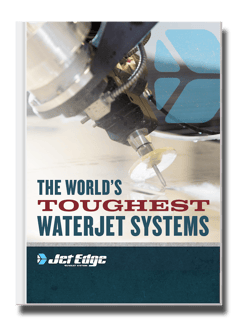
Check Out Our Digital Brochure!
Since 1984, Jet Edge has been designing and manufacturing Ultra-High-Pressure Water jet technology that doesn't back down. Our systems are used around the world in a broad range of industries from the world's leading airlines, to automotive, aerospace and industrial manufacturers, and machine job shops.
To learn more about the Jet Edge difference, our water jet motion systems, pumps and much more, click the button "Download Brochure" to get it now!