Water jet cutting systems rank at or near the top of machine tools when considering the range of materials that can be cut, the high-speed cutting that can be performed, and their high precision capabilities. With fast set up times, high edge finish quality, and the elimination of heat-affected zones that may require secondary grinding operations – they are also some of the most efficient.
An integral element of a water jet cutting system is the catch tank. The material being cut is placed on the catch tank table surface and supported by steel slats. As the cutting occurs, the tank captures the high-pressure water or water/abrasive mix used for cutting and any stock particles or drops created during the cutting process. The catch tank also has a water overflow connection for discharging the process water directly to a drain or a closed loop filtration system.
Sounds straight-forward, right? It can be, but when it comes to catch tanks, you have more choices than you might imagine, so let’s explore.
Catch Tanks 101
The catch tank has two fundamental purposes:
- Provide an isolated, rigid, stable, and perfectly level work surface to support the stock.
- Capture the water used in the cutting process along with the cutting debris and abrasives, if used, AKA the swarf.
Leveling the catch tank ideally takes place during the commissioning of the water jet cutting system. While typical installations occur on stable concrete surfaces, we suggest a routine inspection of the catch tank’s level to protect the precision and accuracy of your cuts.
The structural rigidity of the tank as well as the isolation from the cutting head also impacts cut quality and accuracy. These two characteristics are best achieved in the engineering and manufacturing of the catch tank. Using heavy gauge steel for the construction of the catch tanks provides the highest degree of stability for the workpiece during the cut and will dramatically extend the life of the catch tank. When the gantry and catch tank share common connections or are in any way attached together, vibrations from the gantry’s motion during cutting can transfer to the workpiece and impact cut quality and accuracy. To eliminate this issue, catch tanks should be completely isolated from the gantry.
The illustration below shows the components of a properly engineered catch tank.
Types of Catch Tanks
As previously referenced in this blog, there are more choices in catch tanks than you might expect. When it comes to the major categories of catch tanks, choices fall into standard catch tanks designed to handle water and cutting debris and abrasive catch tanks with additional capabilities in capturing and filtering abrasive particles that make up the swarf.
But, there are variations on the theme of catch tanks beyond standard and abrasive, as the following table illustrates:
Catch Tank Type |
How They Work |
Benefits |
Standard Catch Tanks |
Provide a work surface for cutting and a receptible for the cutting process water and spent abrasive to collect in. |
- Simplest plumbing requirements |
Bladder Catch Tanks |
Incorporates a separate tank adjacent to the catch tank that allows water to flow into. When activated with air pressure, the water is forced back into the catch tank raising its water level. |
- Adjustable water levels |
Active Filtration Catch Tanks |
Equipped with an abrasive removal system that keeps the abrasive suspended as it pulls out the dirty water into a filtering system and then deposits the filtered water back into the tank. |
- Cleaner cutting environment - Minimizes maintenance downtime required to empty a catch tank filled with abrasive. |
Modular Catch Tanks |
Defined cutting sections that may incorporate unique slat layouts or allow for integrating fixtures directly into the tank for reduced setup time and improved repeatability. |
- Optimizes around highest volume cutting methods - May reduce slat wear and replacement costs |
Anti-Turbulence Catch Tanks |
Designed with baffles or features to minimize water movement and turbulence during cutting. |
- Enhances cutting precision on lighter weight material |
Stainless Steel Catch Tanks |
Utilizes a stainless steel tank and stainless steel slats to prevent any rusting and the transferring of marks to the component surface. |
- Eliminate any risk of rust in the tank - Ensures part surface finish quality is not compromised |
Fixed Slat Tanks |
Slats need to be the same height across the work surface to ensure the cutting plane is level. A fixed slat attaches uses fixed mounting holes attaching directly to the catch tank. This limits the range of adjustment that can be made at the slat level. |
- Lower cost when flatness is not a required specification |
Adjustable Slat Tanks |
Slats need to be the same height across the work surface to ensure the cutting plane is level. Adjustable slat tanks allow the cross bar to be adjusted to the plane of the water jet via a cam and bolt. Adjustment for each cross beam makes the leveling of the work surface easier and more exact
|
- Easier to adjust slat height - Change of slat heights can be accommodated through adjustment |
The standard catch tank and bladder catch tank options are selected first and then can be configured to your application by adding any of the additional features outlined in the table above.
Understanding Bladder Catch Tanks
A bladder catch tank enables you to raise and lower water levels in the catch tank to the point where the slats and workpiece submerge. Cutting your stock below the surface of the water dissipates the energy of the cutting jet, thereby reducing spray and dampening the noise associated with cutting without reducing cutting speed, quality, and/or accuracy.
To activate rapid changes in water levels, an air bladder is incorporated into the catch tank with bladder ports cut into one side to accommodate the flow of water in and out of the bladder.
During set up, the catch tank water level remains at a lower level until you are ready to cut. At that point, the operator opens a pneumatic valve, allowing compressed air to enter the bladder weldment - forcing the water out of it and raising the water level in the catch tank for cutting. The catch tank air bladder can be controlled manually with ball valves on the catch tank, electrically with a switch on the controller, or automatically from the controller software.
The water level will rise 2” – 3” depending upon the tank and bladder configuration. It is raised for submerged cutting operations and lowered for material installation and removal.
The Benefits of Submerged Cutting
“My water jet cutting already works exceptionally well, so what does submerged cutting bring to the table, and why should I consider it for my operations?” Here are several process and quality improvements you’ll see from submerged cutting:
Noise Reduction
Precision cutting and machining operations are loud by nature. By submerging the cutting head during the cutting process, you significantly reduce the sound your water jet produces, creating a more comfortable environment for your employees.
Dust and Debris Control
The water acts as an effective and efficient collector of the dust and debris created when cutting in the open air. This capture helps improve air quality around your water jet and directs dust and debris to your bladder catch tank filtration and capture systems.
Reduced Splash and Turbulence
Similar to submerged cutting, the bladder system helps to stabilize the water, reducing splash and turbulence. This is particularly useful in maintaining a clean, accurate cutting environment and stock stability.
Additional Stock Cooling
Lowest temperature cutting process available and is known for zero HAZ effects. However, some materials often benefit from additional cooling by submerging them.
Improved Cutting Accuracy
Submerged stock vibrates less during the cutting process, contributing even more to the accuracy of your water jet cutting system.
Submerged Cutting Pros and Cons
Aspect |
Pros |
Cons |
Noise Reduction |
Significant reduction as water acts as a sound dampener. |
There are no major cons related to noise reduction. |
Debris Management |
Dust and fine particles are captured underwater, reducing airborne contaminants. |
Debris still accumulates in the tank and requires regular cleaning. |
Cutting Accuracy |
Improved by material stabilization and reduced vibrations. |
Visibility is reduced during cutting, making real-time monitoring harder. |
Cooling Effect |
Water naturally cools the material and prevents heat-related distortion. |
May require more water management to avoid contamination. |
Maintenance |
It is easier to clean with less airborne dust. |
Surface areas still need to be cleaned and tank cleaning will be performed when it is filled with debris. |
Operational Simplicity |
Consistent cooling and noise reduction across various materials and cut types. |
Submerged cutting requires time to activate the bladder to fill the tank and lower the water level after. |
Let Jet Edge Help Decide if Bladder Catch Tanks are Right for You
In our experience, we’ve found that practically any water jet cutting system can benefit from adding submerged cutting using bladder catch tanks to the process. However, every situation differs, and there are many variables to consider, including capital costs, desired ROI, maintenance impacts, and expanded material processing capabilities.
So, if you want to learn more about the potential benefits and operational improvements possible from using bladder catch tanks to your operations, contact us today to learn more. You can also call us toll-free at 1-800-JET-EDGE (538-3343), internationally at +1-763-497-8700. Or, if you prefer to do your own research first, we invite you to visit our website, jetedgewater jets.com.
Visit our Blog Library and Comprehensive Video Collection
Click here to view all of our water jet resources in one convenient place!
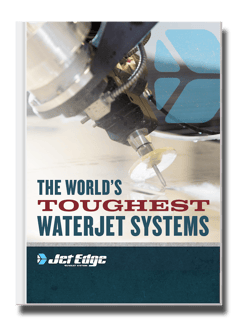
Check Out Our Digital Brochure!
Since 1984, Jet Edge has been designing and manufacturing Ultra-High-Pressure Water jet technology that doesn't back down. Our systems are used around the world in a broad range of industries from the world's leading airlines, to automotive, aerospace and industrial manufacturers, and machine job shops.
To learn more about the Jet Edge difference, our water jet motion systems, pumps and much more, click the button "Download Brochure" to get it now!