Have you ever daydreamed about the added efficiency an extra set of hands could bring to your production operations? The good news is that when it comes to water jet cutting tools, high-rail systems equipped with spreader bars give you that coveted extra set of hands—and more! Let’s explore how you can multiply your water jet cutting productivity with this system combination.
High-Rail Water Jet Motion Systems
Let’s dive into establishing the definition of a high-rail water jet system. All water jet cutting machines utilize a cross beam gantry with a Z-carriage mounted to it. The Z-carriage travels vertically establishing the Z plane of the cutting envelope. The height of the cross beam gantry is what determines the classification of the system as either a mid-rail or high-rail system.
Today, mid-rail motion systems have evolved into the industry standard with common work envelopes of 5’ x 10’ and 8’ x 13’. However, high-rail water jet cutting technology led the way to bringing water jet systems into industrial scale production environments. High-rail motion systems utilize taller legs that are detached from the cutting table to suspend the side rails above the catch tank. This allows fabricators to machine larger stock. The raised gantry design provides easier access to the cutting area and raises critical system components out of the processing environment for protection.
3-Axis Cutting with Precision Machined Spreader Bars
Fabricators rely on 3-axis cutting when the specifications require cutting in two dimensions across the X and Y planes and do not require vertical travel (Z-axis). In most of these applications, the Z-axis the cutting heads are mounted to are fixed in the down position while cutting and return to the up position (material load/unload) position at the end of the cycle.
Spreader bars
A spreader bar is a steel beam mounted to the Z-axis assembly of a high-rail water jet. Spreader bars can be specified in lengths of 2’, 4’, 6’, 8’, 10’ and 12’ and carry up to 12 cutting head assemblies. The assemblies are spaced along the spreader bar manually or from a CNC program when an automated positioning upgrade has been installed. Multiple cutting heads allow you to cut identical parts simultaneously with each cutting head or selected cutting heads. This can greatly increase overall productivity and output of a single water jet system.
Cutting head options
Spreader bars support both water-only and abrasive 3-Axis cutting heads. When combined, this dual capability enables you to switch between water only cutting and abrasive cutting with no setup time. Drills and rotary swivel cleaning manifolds can also be added to perform secondary operations.
Multiplying Water Jet Productivity with High-Rail Spreader Bars
When your project specifies cutting a large number of identical parts from a single sheet or roll, a high-rail spreader bar equipped with multiple cutting heads exponentially increases throughput and overall fabrication efficiency.
- Precision machined spreader bars allow you to mount up to 12 cutting heads or tools on the Z-axis assembly, positioned along the spreader bar to exact positions. When a full spreader bar is deployed, productivity, measured by cycle time per part, can be improved by a factor of twelve.
- Adding a pneumatic drill or rotary cleaning manifold allows secondary operations to be performed during cutting, further reducing costs and production times.
- Three-axis water-only and three-axis abrasive tools can be combined on the spreader bar to eliminate set-up time on material changeovers from water-only to abrasive cutting.
- A motorized sub-Z assembly mounted to the spreader bar allows each tool to be raised and lowered independently an additional 3 inches vertically so cutting heads not in use may be moved away from the cutting surface.
- Each cutting head has a shut-off valve to the ultra-high pressure (UHP) water supply, so heads not in use will not be deployed.
- Since many parts are cut from a single sheet during the cycle time, a material handling system may be incorporated that allows for the cut parts to be removed from the cutting surface and the next blank loaded while a second sheet is in the water jet cutting envelope, a capability that reduces downtime required to replace stock.
Jet Edge Can Help - Customer Success Stories
A success story can provide additional information, stimulate curiosity, and answer questions you hadn’t considered before. To help you, here are several case studies demonstrating the capabilities and efficiency improvements possible with the use of spreader bars.
Jet Edge Water jet System |
High-rail Work Envelope |
Z-package Specifications |
Case Study Link |
Edge X3 |
6’ x 10’ |
|
|
Edge X3 |
12’ x 12’ |
|
|
Edge X3 |
6’ x 6’ |
|
|
Edge X3 |
6’ x 12’ |
|
|
Edge X3 |
4’ x 4’ |
|
Jet Edge has hundreds of successful installations under its belt and can walk you through using high-rail systems and spreader bars to enhance your water jet productivity and give you that extra pair of hands you’ve been longing for.
Contact us today to learn how to increase the services you offer your customers and reduce costs through enhanced productivity. You can also call us toll-free at 1-800-JET-EDGE (538-3343), internationally at +1-763-497-8700 or visit our website jetedgewaterjets.com to learn more.
Visit our Blog Library and Comprehensive Video Collection
Click here to view all of our water jet resources in one convenient place!
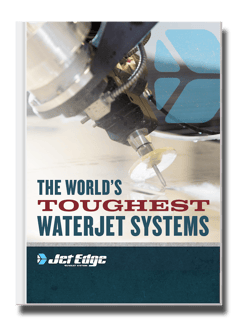
Check Out Our Digital Brochure!
Since 1984, Jet Edge has been designing and manufacturing Ultra-High-Pressure Water jet technology that doesn't back down. Our systems are used around the world in a broad range of industries from the world's leading airlines, to automotive, aerospace and industrial manufacturers, and machine job shops.
To learn more about the Jet Edge difference, our water jet motion systems, pumps and much more, click the button "Download Brochure" to get it now!