Robotic water jet cutting is just what it sounds like, the integration of the water jet’s unique and flexible cutting characteristics with the productivity and precision capabilities of robotics. Pairing these two technologies creates a cutting, finishing, material handling, and/or cleaning solution that enables you to produce complex parts and/or processes across a wide platform of operations both accurately and efficiently.
The Short Story of Water Jet Cutting
Water jet cutting systems take an incoming water supply and bring it up to ultra-high pressures (60k – 87k PSI) using intensifier pumps (some systems use direct drive pumps, for more on this, check out this blog examining the difference). This high-pressure water stream is then directed to a cutting head or cleaning swivel mounted to motion system gantries, robot arms, or slitting lines based on the application. This stream is directed by a CNC program and results in very precise cutting accuracy and high-quality surface finishes.
Many materials can be cut simply using the high-pressure water. Water-only cutting works especially well when machining soft or flexible materials like rubber, plastic, foam, and textiles. When abrasive is introduced into the water stream, it exponentially expands the types of materials you can cut. This includes composite materials, aluminum, glass, stone, ferrous and non-ferrous metals, and specialty alloys like stainless steel, titanium, and Inconel.
A variety of 3 axis and 5 axis cutting heads can be mounted on the motion system’s gantry. The cutting table, often referred to as a catch tank, can range in size from 4’ x 4’ to 13’ x 24’ depending upon the size of the raw material and the characteristics of the finished parts. CNC software controls the motion of the cutting heads along with drives that deliver the accuracy and repeatability of the system.
Robotic Water Jet Cutting and Cleaning Applications
Despite the advantages and efficiencies of these systems, the water jet head/gantry/table combination can be limiting in specific applications. Specifically, there are times where a water jet cutter would deliver a better total production result, but gantry and/or table could be a deal breaker. In these applications, freeing the cutting heads from the table and gantry by attaching them to robotic arms enables you to execute significantly more complex processing steps and cutting profiles. Two common applications of robotic water jet cutting applications are explored below.
Robotic Trim Cells
Many parts are formed by methods other than cutting. Some examples include casting, molding, forging, and stamping. These parts share some common characteristics such as seams, sprues, excess material, flashing, etc. that need to be trimmed away to achieve a finished appearance. The trimming process often takes place in small, dedicated workspaces called trim cells.
Softer materials like rotational molded plastics are commonly trimmed using router bits. Fiberglass and ceramic might be trimmed with saws or grinders. In many other cases, the solution involves manual finishing using material removal tools like sandpaper, rasps, and files. These types of trim cells tend to be very labor intensive and may create safety concerns for operators.
Enter water jet trim cells. When a water jet cutting head is attached to a robotic arm, the need for routers and hand trimming operations is eliminated. Robotic water jet trim cell cutting involves securing a workpiece to a fixture that holds the part in place. The robotic arm then moves around the part freely, utilizing the water stream to execute the trimming cuts. The water jet robotic arm is not constrained by the 3 axis or 5 axis cutting that is done on a motion system table.
To see this in action, check out how Alliance Automation integrates Jet Edge intensifiers with their trim cell solutions to meet the needs of automotive manufacturers.
Robotic Cleaning Cells
Water jets have other often overlooked uses such as cleaning, degreasing, and stripping. When surface contaminants need to be removed, water jet cleaning offers a unique solution. In these applications, sometimes referred to as water jet stripping or water jet blasting, the goal is the removal of all grease and old coatings with no removal of the substrate material.
There are many benefits to using water jet systems for these applications. When using water systems, solvents and other harsh chemicals are not required as the power of water removes the material. When a water jet cutting head is adapted with a cleaning swivel and attached to a robotic arm, only the surfaces requiring cleaning are traced. The focused pressurized water stream replaces the need for manual cleaning and the use of corrosive chemicals. All of these processes take place in a purpose built chamber with various fixtures used for parts hold down.
For an example of this in action, check out how Progressive Surface uses Jet Edge water jets in these applications.
ROI for Robotic Cell Applications
The robotic cutting and cleaning automation processes emphasize reducing or eliminating processing time. However, there are many additional potential benefits including eliminating secondary operations, automating repetitive tasks, improving process quality, reducing the risk of operator injury, increasing production throughput, and/or expanding unattended cutting capabilities.
Automated Material Handling Systems in Water Jet Cutting
Automation is pervasive on the material handling side of production systems. Pick and place systems, sorting, conveyors, etc. are very commonplace. Opportunities for increased efficiency exist in the integration of automated or semi-automated material handling systems into your water jet cutting. Three common types of material handling systems are detailed below.
Pick and Place Robotic Systems
This automation solution may be the most familiar to you. Companies regularly show videos of these mechanical marvels working with unwavering precision to move parts between the processing stations that perform a production step. Automation in the form of robots at work conveys a message of high-tech, precise, leading edge, and high-quality manufacturing processes.
In the most common application, robots pick a workpiece or part from a stockpile and place it on a work surface in position for cutting. The water jet cutting head then passes along the piece and cuts it to shape, creating the required profile and finish. At the end of the cutting cycle, the robotic arm moves the finished part to the next production stage, picks another part, and repeats the process. If the robotic arm/water jet cutting head combination has a steady supply of parts, it can run unattended, or with minimal labor, 24-hours a day.
Inline Automated Conveyor Systems
Inline conveyor systems are another common automation solution especially in continuous slitting and cutting processes. These are common to foam, paper and textile production. The manufacturing process revolves around the conveyor with raw materials entering one end and finished products exiting the other. Once a part or nest of parts has been processed, the conveyor advances the completed piece and brings in the next workpiece blank to the cutting table. The high-rail system illustrated, has four water jet cutting heads mounted on a custom spreader bar for increased productivity and throughput.
Semi-Automatic Cart Load/Unload Systems
Some materials require different handling methods because of part sizes, material flexibility, or material fragility. A case in point is the medical device foam packing material manufactured by Merryweather Foam. Demand for their products meant working expensive overtime shifts to fill customer orders. Their existing process required workers to stop the cutting equipment, load and/or position stock, take measurements to ensure accuracy, start the cutting system, remove the cut parts, and repeat. This process limited the utilization of the cutting system and limited output. The illustration and linked case study shows a high rail cutting table with eight water jet cutting heads mounted inline. The head spacing was automated using a docking system that positioned the heads based on the program being run.
To improve machine productivity and throughput additionally, they specified a dual cart solution to feed stock material to the cutting system on one side, and while the machine cut parts, the finished parts where removed at the other side. The carts were manually positioned. At the start of the cutting cycle they were locked in place and pneumatically raised to a cutting position. This ensured flatness of the material across the table. This system can be duplicated in any number of facilities.
Empower Your Operations with Robotics, Automation, and Water Jet Cutting Systems
Whether your automation goal is productivity, process improvement, throughput, safety, or all the above, Jet Edge can help you. We’ll work with your team to adapt our systems to your specific cutting, trimming, and surface preparation operations.
Contact us to talk with an application engineer about your product or application. We’ll perform an application analysis to get the discussion started. Visit our Case Study library to see more custom applications and how collaboration with the Jet Edge engineering team delivered a solution that optimized their water jet cutting operations.
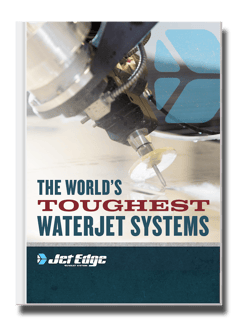
Check Out Our Digital Brochure!
Since 1984, Jet Edge has been designing and manufacturing Ultra-High-Pressure Water jet technology that doesn't back down. Our systems are used around the world in a broad range of industries from the world's leading airlines, to automotive, aerospace and industrial manufacturers, and machine job shops.
To learn more about the Jet Edge difference, our water jet motion systems, pumps and much more, click the button "Download Brochure" to get it now!