According to an article by TWI, a composite material is:
"a combination of two materials with different physical and chemical properties. When combined, they create a specialized material to do a certain job, for instance, to become stronger, lighter, or resistant to electricity. They can also improve strength and stiffness. Companies develop and use these materials instead of traditional materials because they improve their base materials' properties and are applicable in many situations."
What are Composite Materials?
Surprisingly, composite materials are far older than many people realize. The Mesopotamians engineered plywood in 3400 B.C, the first composite material. A millennium later, the Egyptians fabricated death masks by soaking linen and other materials in plaster in 2181 B.C. And the Mongols created the predecessor to the modern composite bow in 1200 A.D. Today, the most recognizable composites include fiberglass, carbon fiber, composite foams and plastics.
A significant issue with composites is their sensitivity to heat and edge deformation during the cutting process. This sensitivity typically rules out laser and plasma technologies because of their heat-based cutting methodology. Also, CNC machines may generate unacceptable heat levels, depending upon the composite, speed of cut, cut geometry and more.
Because of the limitations of other cutting technologies, the water jet is often the best option when you need to cut a composite. Let's explore the reasons for this.
Unconventional Materials Require Different Cutting Solutions
Each of these materials has its own unique requirements for machine setup and cutting head selection. Cutting speed is important in advanced plastics to avoid heat deformation at high speeds or delamination at lower revs. Some materials dull cutting tools faster. Uncorrected, dull heads can reduce accuracy down the line and increase manufacturing costs through waste and increased tool replacement costs.
Depending on the design, materials may be heat-treated before machining to allow higher levels of precision but, this increases the material’s hardness thereby increasing the machining difficulty. The heat produced during machining can negatively impact the heat treatment causing the component to fail to meet specifications. A solution is to machine the parts prior to heat treatment. However, post-machining heat treatment can affect accuracy.
Consistently Superior Edge Quality
The very nature of composite materials contributes to their cutting characteristics and resulting challenges. Take, for example, carbon fiber. This product consists of strands of various carbon fibers woven together, treated with binding chemicals and baked in industrial ovens.
Imagine the cross-section of carbon fiber and what the edge looks like. Then compare that to the cross-section and edge of metal. If you envision a somewhat fibrous, uneven edge versus a homogenous, smooth edge, you see one of the cutting challenges.
Water jets deliver the same pristine cuts in composite materials as in metals, eliminating fiber pull, delamination and never create a heat affected zone (HAZ). This is particularly relevant when cutting laminate glass and laminated glass composites. Heat can strip these products of their crucial laminates resulting in the product being unusable.
Fiber Pull
When cut, carbon fiber (and other fiber composites) materials can experience fiber pull, resulting in stray strands (whiskers) along the cut edge. If the final use requires a whisker-less edge, follow-up work is required, adding cost. Whiskers are not an issue with water jets which leave a smooth, strand-free edge, a clean shave, in other words.
Delamination
Layered and woven composite materials are susceptible to delamination during cutting. In fact, it is one of the most frequent complaints about composite edges. Delamination is especially problematic when drilling and piercing (non-linear paths) holes inside a composite part. There are two types of delamination: peel-up, which occurs on the top of the material as the cutting tool enters and push-down on the bottom as the bit exits.
Delamination's root cause can be from the cutting tool's heat breaking chemical bonds, cutting tool pressure breaking mechanical bonds and other factors. Heat-related delamination isn't an issue with water jets' cold cutting technology. Hole cutting and piercing-related delamination are readily overcome by adjusting the cutting pressure to accommodate the material's characteristics.
No Heat Affected Zones
Water jet technology is, by nature, cool and, therefore, does not impart any cutting-generated heat to the material surrounding the cut. Heat affected zones (HAZ) develop when the cutting technology imparts process heat to the material adjacent to the cut, altering the material's properties. Especially crucial in the aerospace industry, HAZ can be an issue for any of your customers. HAZ impacts include additional post-cut processing and increased material waste.
Minimal Waste
A characteristic of water jets is their minimal kerf. This characteristic enables you to nest parts within 1 mm of each other, provide highly detailed cuts, significantly reduce material waste, and maximize stock utilization and efficiency with "near net" cutting.
Material Versatility and Efficiency
Water jets can be your "Swiss Army Knife" production floor cutting tool when it comes to composites. Regardless of the material, there is a nozzle, water pressure and grit combination that delivers the specified cut quality. What does this mean to you? Versatility handling a wide range of materials from carbon fiber to fiberglass to plastics and more. Your water jet cuts it all with a single system, eliminating specialty tools designed for a particular material type.
Cut Up to 10" at a Time
Water jets are capable of cutting some composites up to 10" thick. In practical terms, this enables you to stack sheets of thin material and cut multiple parts simultaneously, reducing production time. Also, you can cut single sheets of greater thicknesses. Using a single water jet system, you increase production throughput, reduce waste and expand the range of materials you can cut for your customers.
Talk to Jet Edge
Contact us today to learn how to introduce or expand composite material cutting to your service offering. It is an excellent way to increase your opportunities and grow your business. You can also reach us by phone toll-free at 1-800-JET-EDGE (538-3343) or internationally at +1-763-497-8700.
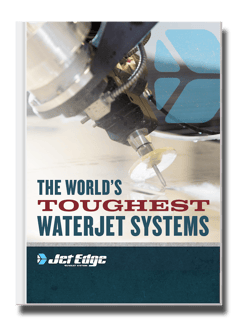
Check Out Our Digital Brochure!
Since 1984, Jet Edge has been designing and manufacturing Ultra-High-Pressure Water jet technology that doesn't back down. Our systems are used around the world in a broad range of industries from the world's leading airlines, to automotive, aerospace and industrial manufacturers, and machine job shops.
To learn more about the Jet Edge difference, our water jet motion systems, pumps and much more, click the button "Download Brochure" to get it now!