The first water jet cutting system can be traced all the way back to the mid-1800s when miners used high-pressure water to remove overburden in hydraulic mining operations. While crude by today's standards, it is notable for being the first industrial process using water to erode and remove material.
By the 1930s, the technology had evolved to the point that it could accurately cut paper and soft materials. Following World War II, interest in water jet systems grew as companies investigated alternative, more efficient cutting technologies. By 1956, high-pressure, water-only systems were cutting plastics and similar materials. Finally, in 1958, the first water jet systems capable of cutting hard materials like aerospace-grade stainless steel made their way into production facilities.
Research into mixing abrasives with water started in 1935, but it wasn't until 1984 that a paper was published covering the technology and in 1986, the magazine, Mechanical Engineering published a longer list of materials abrasive water jets could cut, including titanium, aluminum, glass and stone.
The ever-growing list of materials water jet systems could process led to widespread adoption in practically every industry. Factor in the integration of CAD/CAM capability in recent years and you now have arguably the most versatile cutting solution available. Where it was common 30 years ago for people to say, “You can cut that with water?!," today is common to hear, "You produced that 5-axis cut with those beautiful edges using water?!." Yeah, you can cut that with water jet systems.
The Materials You Can Cut with Water
It might be easier to list the materials water jet systems cannot cut but to generalize, you use water as an alternative to heat to cut your material. With that in mind, we will review a range of materials routinely processed with water jet cutting solutions to show the versatility these tools bring to the shop floor.
Metals and Specialty Alloys
Early development of water jet cutting systems involved processing commonly use metals such as aluminum, steel and stainless steel. These materials can be dense and thick requiring intense heat, which may distort the material properties or require secondary operations to grind surfaces down to a higher finish quality. Today, modern abrasive water jet cutting solutions are used when a heat-affected zone distorts the metal properties, especially when cutting aluminum block, thick stainless steel stock, specialty titanium alloys and Inconel. For more information on metals cutting visit our Cutting Titanium, Stainless Steel and Other Specialty Alloys technology page or read our blog on the topic.
Glass
Cutting glass with a water jet system perfectly showcases the capabilities of these tools. As a “cool cutting technology”, water jet systems cut cleanly without creating a heat-affected zone (HAZ) or leaving a rough edge requiring additional processing steps. With the proper combination of pressure and abrasive, a water jet can cut standard, laminated and thick bullet resistant glass. The resulting cuts are smooth as glass (pun intended) and can be straight, curved or beveled. We invite you to learn more about the unique requirements of cutting glass and how to tackle them with water jet systems.
Carbon Fiber and Laminated Materials
More and more of our customers are being asked by their customers to cut carbon fiber and other laminated materials. And because of the benefits of these materials to manufacturers, the opportunity to grow your business into another sector is enticing.
However, these materials present unique challenges of their own. Multi-directional fibers cut with ordinary tools can leave whiskers and cutting zone damage including delamination. Removing whiskers needs a secondary step adding time and cost to part production. HAZ damage can lead to increased scrap losses, another cost you can avoid with water jet systems. We have more to say about composites here.
Foam
Yes, water jet systems can cut a variety of foam types. Foam by its nature is sensitive to heat and the potential for edge damage from heat-based cutting tools. With the correct pressure, grit and CAD drawings and CAM instructions, even complex shapes are possible. An excellent example of our systems cutting foam is the solution we developed for Merryweather Foam, a foam packaging company servicing the medical device industry. You can read the case study here.
Textiles
Cutting fabrics and textiles with water jet systems has a long history, being one of the earliest materials processed with these tools. Today, water jets are being used to cut an exceptional range of textiles in industries as diverse as automotive and aerospace. Cutting heads are often mounted to robotic arms for trimming or are fixed to a surface with a conveyor running underneath for slitting. These water jets can cut headliners, seating foam, interior fabric and carpeting creating a finished edge with a single cut, eliminating the need for expensive stamping dies or consumable blades. To see water jets in action in the automotive world, read our Alliance Automation case study.
Plastics, Rubbers, Acoustical Foams, Food and Many More Items
Water-only cutting is used across a gambit of materials including plastics, rubber, acoustical foam, food and more. When heat is an issue in the cutting process, many turn to waterjets. Once again, the cool cutting of water jet systems provides exceptional single-cut edge finishes, minimizing stock loss due to heat deformation.
What Did We Miss?
Did we mention stone, pipe, cement…Even though this is an abbreviated list of materials, it illustrates the versatility of water jet cutting systems. From soft foams to plastics to exotic alloys and metals, all can be cut by the combination of pressure, water and abrasive.
Water jet cutting solutions are the only tools with such a wide range of applications and material handling versatility. But the question is, why are these solutions so adaptable and capable? Many developments have come together to position the water jet as the premier cutting tool. Advances in nozzle design and durability, development of dependable extremely high-pressure pumps, a wealth of grit sizes and CAD/CAM-driven control combine today to give you the finest cutting tool available.
Talk to Jet Edge to Learn if Your Material Can Be Cut with Water
Since 1984, Jet Edge has been designing and manufacturing Ultra-High-Pressure Water jet technology that doesn't back down. Our systems are used around the world in a broad range of industries from the world’s leading airlines to automotive, aerospace and industrial manufacturers, and machine job shops.
This article will continue with part 2 of the series...
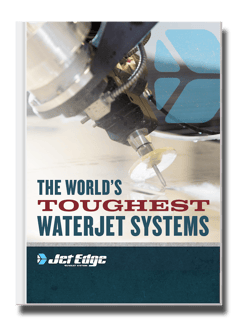
Check Out Our Digital Brochure!
Since 1984, Jet Edge has been designing and manufacturing Ultra-High-Pressure Water jet technology that doesn't back down. Our systems are used around the world in a broad range of industries from the world's leading airlines, to automotive, aerospace and industrial manufacturers, and machine job shops.
To learn more about the Jet Edge difference, our water jet motion systems, pumps and much more, click the button "Download Brochure" to get it now!