NOTE: This post was originally published on January 14th, 2022 and has been updated on July 11th, 2025
Every industry that requires precision-machined parts has its own set of unique manufacturing challenges. But it's safe to say the aerospace industry is especially challenging and demanding. Parts manufactured for the aerospace industry invariably require:
- Extremely tight tolerances
- Extraordinarily complex shape geometries (5-axis vs 3-axis)
- Specialty materials with out-of-the-ordinary properties
- Small production runs
- Short-notice ordering
- Fines for out-of-spec parts or late deliveries
- Elevated exposure to the repercussions of part failure
In an industry where failure can mean loss of life, aerospace manufacturers operate under intense scrutiny, regulatory oversight, and potential liability. Water jet cutting offers a safer, smarter solution by delivering precise, repeatable cuts without introducing heat-related distortion, material stress, or compliance concerns. In aerospace and defense, "close enough" results aren't “close to good enough.
Post Contents
The Aerospace Manufacturing Challenge......................................................2
Specialty Materials & Their Machining Hurdles............................................2
-Unconventional Materials Require Unconventional Cutting..................2
Flexible Tooling for Variable Part Sizes and Designs...................................3
-Repeatability, Nesting & Short-Run Production.......................................4
-Speed of Manufacture.................................................................................4
-Rapid Prototyping Capabilities....................................................................4
Certification and Aerospace Compliance......................................................5
Digital Manufacturing Integration..................................................................5
Cost Advantages Over Other Cutting Methods............................................5
Environmental & Safety Benefits....................................................................6
Multi-Sheet Stacking and Batch-Cutting........................................................6
5-Axis Cutting for Complex Aerospace Geometry.......................................6
Let's Talk About Your Aerospace Needs.......................................................7
The Aerospace Manufacturing Challenge
Manufacturing parts and components for the aerospace industry pushes the precision capabilities of your processes and tooling to the limit. Failure to meet any parameter or specification can lead to the rejection of the entire production run. At best, this may require rework. At worst, it may result in heavy fines and the scrapping of the parts.
The bottom line is this: aerospace parts demand exceptional precision in extremely difficult-to-machine materials and carry exceptional risk. Tolerances on critical components often reach ±0.001 inches or tighter, particularly for engine parts, fasteners, and moving mechanisms. Missing these specs isn’t just costly, it can be catastrophic.
Specialty Materials & Their Machining Hurdles
Due to the extreme environments and stresses placed on these parts, the aerospace industry utilizes specialty materials that exhibit unique properties, including strength, weight, heat resistance, dimensional stability in extreme temperatures, and corrosion resistance, among others.
When looking at the specific materials required for aerospace part fabrication, corrosion-resistant super-alloy materials like Inconel, Hastelloy, Waspaloy, and MP35N, aerospace grades of aluminum (7075, 2024, and 6061), stainless steel, steel alloys (4140 and 4340), nickel-titanium (Nitinol), titanium (Grades 2 and 5), advanced plastics (PEEK, UHMW, Ultem®), and composites are common.
Each of these materials presents its own set of machining challenges, including heat sensitivity, brittleness, thermal deformation, and excessive wear on the cutting tool heads (where the heads make direct contact with the material). As a result, aerospace parts providers have the choice of using multiple cutting technologies or simplifying their operations with the all-material capability of a water jet cutting system.
Unconventional Materials Require Unconventional Cutting
As many aerospace materials are selected specifically for their material properties, it is important to ensure that the manufacturing process does not alter these properties. As an example – thermal processes can create a variety of defects that can be extremely detrimental. Metallurgical effects like Heat Affected Zone (HAZ), generation of recast or remelt as well as oxide layers, and hot cracking (cracks caused due to stresses induced from non-uniform heating) are all side effects of thermal cutting processes. Additionally, heat input can affect dimensional tolerances, cause cosmetic defects, and create distortions in the work piece.
While all materials are susceptible to heat damage during machining, some are more susceptible than others, and for certain applications, these detrimental effects are absolutely unacceptable.
Lasers and plasma cutters are the obvious offenders in this area because they use heat to cut, however, even traditional CNC machine tools generate heat which can damage the part and or change material properties.
Water jet cutting on the other hand is an inherently non-thermal process. Given this, it eliminates concerns about heat damage to the work piece during machining, making it an ideal process when metallurgical properties are important.
Another challenge presented is that each of these specialty materials has its unique requirements for machine setup and cutting head selection. For example:
- Proper cutting speed is critical in advanced plastics and composites to avoid heat deformation at high speeds or delamination at lower revs.
- Some materials dull end mills and insert-style cutters faster. Uncorrected, dull cutting heads can reduce accuracy down the line and increase manufacturing costs through waste and increased tool replacement costs.
- Depending on the part's design specifications, stock materials may be heat-treated before machining to allow higher levels of precision, but this increases the material’s hardness, thereby increasing the machining difficulty. The heat produced during machining these materials can negatively impact the heat treatment, causing the component to fail to meet specifications. A solution is to machine the parts before heat treatment. However, post-machining heat treatment can affect accuracy.
- Brittle and fragile materials require special attention to the cutting speed, angle, and direct pressure from the cutting head.
Water jet systems address and solve all of these challenges in a single machining solution.
Flexible Tooling for Variable Part Sizes and Designs
The number of parts an airplane or launch vehicle requires can be staggering, as can the range of sizes and shapes that these components come in. From a tiny screw to a landing gear strut, producers of parts for the aerospace industry must have the tooling flexibility to produce a wide range of components.
Flexibility can be achieved by purchasing dedicated tooling for a specific material or component. Given the small runs common in the aerospace industry and the rapid pace of design and material evolution, this approach is expensive and potentially risky. In addition, dedicated machinery consumes valuable floor space, requires additional training, and has maintenance requirements, all attributes that increase costs for the company.
There is a proven answer to the manufacturing demands of this industry: water jet cutting. This cutting process is the only solution that can deliver these capabilities:
- Any aerospace material can be cut without the side effects of heat deformation or delamination.
- Cut precision equals or exceeds many, if not most, other machining technologies.
- First-cut surfaces are finer and reduce or eliminate post-production clean-up.
- Complex, 5-axis cuts are possible in addition to simpler 3-axis cuts.
- Issues with cutting tool wear on accuracy and costs are virtually eliminated.
- Able to handle both small and large components using the same machine.
- Reduced training and maintenance costs because one machine does the job of several.
Repeatability, Nesting & Short-Run Production
It is common for aerospace components to have frequent small-quantity production runs. If you have the contract to manufacture these parts, this means more setups and tooling changes will be required when you receive future orders.
So, once the CNC tooling parameters are set and meet all engineering specifications, being able to load that setup for each future run is a tremendous benefit. It reduces prep time and allows you to provide your customers with a faster turnaround. It also reduces production costs and risks.
But how confident are you that reloading the last successful setup program will produce the same results? As already mentioned, machine and cutting tool wear can impact accuracy. Did the tooling develop any wear while turning out other parts that might affect accuracy now? Unless the tool sits idle between runs, you may incur additional setup time to ensure the tool can deliver the same results.
Once the parameters are dialed in, the setup for the next run is faster. Not changing tooling instructions also eliminates the potential for error. water jets deliver shorter setup times, rock-solid repeatability, and unwavering accuracy.
Speed of Manufacture
Water jets are ideal for small-run quantities and high-mix environments. No custom tooling or cutting heads are required, so procurement delays for specialty equipment aren't an issue. You acquire the specified material for the part, select the proper orifice or nozzle, load the correct abrasive for the cut (not required for water-only cuts in softer materials), program the tool, and start machining. All this leads to reduced setup times and a corresponding shortening of order turnaround.
And if your water jet solution has 5-axis capability, managing part complexity is a significantly reduced issue. Facing the need to produce large parts, small parts, simple or complex, or small-lot production? Water jets are the most versatile tools you can place on your production floor.
Rapid Prototyping Capabilities
Water jet systems offer the fastest time from CAD concept to finished part. When engineering teams constantly innovate and modify designs and materials to achieve performance and competitive advantages, being able to turn a potential innovation into a finished part quickly is a critical advantage.
The capability of prototyping components in days rather than months allows aerospace engineers to experiment with different materials and design combinations. With physical samples in hand, they can test them to see which combination best meets design requirements.
water jets thrive in this environment for all the reasons mentioned in the preceding section. With no specialty cutting heads or custom jigs required to fabricate the prototype, your shop can give your customer’s engineers the ability to test multiple materials and geometries almost on the fly. Speed and capability like this can offer your customers a decisive advantage, making you their vendor of choice.
Certification and Aerospace Compliance
Aerospace part manufacturers operate under rigorous quality standards, such as AS9100 and ISO 9001, which require full production traceability, unwavering repeatability, and detailed documentation for every part produced. Each cut, dimension, and material selection must be auditable and defensible, particularly when working with defense contractors or commercial original equipment manufacturers (OEMs).
Water jet systems support these requirements by offering precise, programmable cuts, digitally logged operations, and consistent results across production runs, which makes it easier to maintain certification, pass audits, and meet the high bar of aerospace compliance. Jet Edge water jet systems are built with these exacting standards in mind, helping manufacturers stay audit-ready while delivering aerospace-grade quality at every stage.
Digital Manufacturing Integration
Jet Edge water jets thrive on digital control. We design our systems to accommodate digital design and control parameters. The IGEMS CAD/CAM package is widely regarded as the premiere software package in the water jet cutting industry. IGEMS enables seamless file imports from major software products, including SolidWorks, Fusion 360, AutoCAD, and others. With this capability, our cutting systems support a variety of file formats, including .IGS, .STP, .DXF, and .DWG among others.
Our solutions offer real-time cut monitoring, enabling immediate issue response, and are compatible with factory floor automation and Industry 4.0 initiatives, including data acquisition, production traceability, and remote programming.
Cost Advantages over Other Cutting Methods
Water jet solutions deliver significant cost advantages over alternative cutting methodologies for one simple reason: they can cut every material commonly used in the manufacture of aerospace parts. The alternative? Multiple cutting technologies to handle different materials. That means higher costs and increased complexity. With water jet cutting solutions, you enjoy lower costs because:
- Eliminate the negative side effects of thermal processes.
- No need for tool sharpening or replacement.
- Lower scrap rates due to precision and nesting.
- One machine handles multiple materials and part types.
- Reduced or eliminated secondary operations for cut surfaces.
- Support for a lights-out production model expanding your manufacturing capacity.
Environmental & Safety Benefits
Water jets eliminate or dramatically reduce environmental impacts by design. Let’s explore a few of the reasons for this environmental friendliness:
- Water and abrasives can be captured and reused. Spent abrasive can be repurposed for use in other industries or cleaned and disposed of safely in landfills.
- Airborne particulates are substantially reduced as the water jet captures them and carries them to the catch tank.
- Eliminates the toxic fumes or harmful VOCs from materials when cut with thermal processes like lasers and plasma.
- Maximized stock utilization conserves scarce material resources.
- Requires significantly less energy when compared to laser, plasma, and some direct contact cutting solutions.
- Superior first-cut edge finishes can reduce or eliminate secondary finishing steps that are labor intensive and often ergonomically challenging.
Multi-Sheet Stacking and Batch-Cutting
Thinner materials can be stacked and cut successfully with a water jet. Think of the cost savings (reduced cost per part) and production throughput efficiency improvements you can realize by cutting multiple parts simultaneously. Material stacking and batch cutting can be especially useful when fulfilling orders for aerospace kit builds or subassembly packaging.
5-Axis Cutting for Complex Aerospace Geometry
The current generation of water jets from Jet Edge has a 5-axis option for the most demanding and complex cuts. These cutting heads enable you to cut bevels up to 60 °, chamfers, and complex contour cuts to match the modern complexity of aerospace components. Cutting the entire part in one pass reduces the need to move parts to different equipment for specific profile cuts and edge finishing.
Let's Talk About Your Aerospace Needs
Water jet cutting solutions are ideal for the unique demands and challenges of the aerospace industry. A water jet can cut all the unusual materials commonly used to fabricate aerospace parts, accommodate the most complex designs, facilitate rapid prototyping, thrive in a high-mix manufacturing environment, and provide numerous critical benefits such as never producing thermal defects like HAZ, delivering rock-solid repeatability, and more. Adding a water jet to your operation provides a tool essential for meeting the needs of aerospace manufacturing today and in the future.
If you're looking to improve your processes for manufacturing components for your aerospace industry customers, or are considering entering the market, talk with Jet Edge today. We have extensive experience in the aerospace market, we understand the critical and unique challenge faced by manufacturer’s of aerospace components, we offer the most advanced 5-axis water jet systems on the market, and we stand ready to support your success now and for the decades you will own your Jet Edge equipment. We are great “Partners in Aerospace”!
Contact us or fill out the form below to download our brochure. We'd love to start a conversation on how we can improve your bottom line.
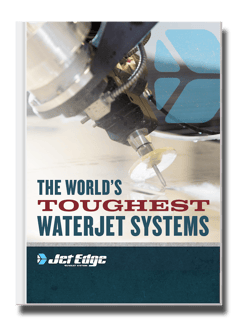
Check Out Our Digital Brochure!
Since 1984, Jet Edge has been designing and manufacturing Ultra-High-Pressure Water jet technology that doesn't back down. Our systems are used around the world in a broad range of industries from the world's leading airlines, to automotive, aerospace and industrial manufacturers, and machine job shops.
To learn more about the Jet Edge difference, our water jet motion systems, pumps and much more, click the button "Download Brochure" to get it now!