Water jet cutting machines offer a range of productivity options to increase throughput. For example, a dual-carriage mid-rail CNC water jet utilizes two carriages to double team a single part or cut two like parts at once. A high-rail water jet cutter can incorporate up to 10 cutting heads along a precision spreader bar for 10x production rates. Lights out cutting can be added to either system and allows an operator to set up the water jet and walk away as garnet flow and water pressures are metered to ensure uninterrupted production. IGEMS nesting software can be used for common line cutting to allow for multiple like or unlike parts to be cut from a single program minimizing set up and maximizing material utilization.
A lesser-known option that works with some material types is cutting stacked material with your water jet. This article will provide some helpful tips and cautions as you explore this option for your material.
Stacking Materials for Water Jet Cutting
As the name suggests, stacked materials involve stacking pieces of stock together during cutting. This is done by securing them on the cutting table and executing the cutting program.
But what are the details around creating the stack? How thick can the stack be? What materials lend themselves best to stacking? Can you stack unlike materials together? Let’s examine each of these questions in turn.
Choosing Stack Height
Measuring the time it takes to cut a single part in the material thickness and contrasting that with the time it takes to cut the stacked parts is critical. The thicker the stack, the slower the cut time so some measurements are required to get the optimum balance. An article in thefabricator.com suggests stacking is best utilized with thinner material and stacking no higher than 0.6”. The best thickness for a particular project depends upon the type of material and the part complexities - especially concerning corners and requires some trial and error.
Best Materials for Stacking
Any material can theoretically be stacked and cut by a water jet. However, it is most commonly used for stacking thin metal material, foam panels and composite materials. One user posting to CNCzone.com said their shop most frequently cuts stacks of 0.02” aluminum stacked to a maximum thickness of 0.375”. This yields the best results in speed of cut, edge finish, and minimized V-shaped taper. The post further states they do not stack materials with a thickness greater than 1/8”.
Stacking Different Materials
As previously stated, you can theoretically stack any combination of materials. However, trial and error will likely be required to optimize cut time and part finish quality. Gluing the dissimilar materials together prior to cutting generally works best. One example would be gluing foam to the back of hard plastic before cutting. This produced the finished part in fewer steps than cutting each material separately and gluing them after the cut process.
Benefits of Cutting Stacked Materials
Cutting stacked materials provides the following benefits:
Increased Production Output
Cutting stacked material produces multiple parts in a single pass, multiplying your production run’s output by the number of sheets in the stack.
Reduced Setup Time
Stacking stock sheets reduces the production run's setup time, again by the multiple of the number of sheets in the stack. This reduces setup labor costs and imposes fewer hours of operation on your water jet.
Uniformity and Consistency
Cutting multiple parts simultaneously produces identical parts, improving your production run’s uniformity and consistency. While the CNC program governs the cutting process, setup errors across cutting individual sheets can lead to part variations.
Energy Efficiency
Cutting more parts simultaneously uses less energy than cutting each sheet individually. These energy savings reduce the production costs for that run.
Lights-Out Cutting
Combining lights-out cutting with stacked materials dramatically increases the economic benefits of an already cost-efficient production process.
What Are the Potential Issues with Cutting Stacked Materials
Here are the top items to consider when cutting stacked materials:
Reducing V-shaped Tapers
The water jet cutting stream loses strength as it cuts through each layer in the stack. This may result in a kerf wider at the top than at the bottom, creating parts with different dimensions. You can mitigate the possibility and severity of the V-shape taper by reducing the stack thickness and slowing cutting speed or cutting with taper compensation on your cutting head.
Accommodating Part Complexity
The more complex the cut, the less benefit stacked materials offers. When precision cuts are required, many pierces or there are multiple sharp corners cut speed needs to be reduced. A time study will need to be completed to evaluate stacking versus single piece cutting.
Maintaining Stack Alignment
Stacked material, if it is not held down, may shift during the cut producing unacceptable results. A hold down method needs to be developed to avoid shifting. The most common methods would be weight being placed on the workpiece, a clamping system or securing the stack with a fastener.
Determining the Best Stack Thickness/Cutting Speed Combination
When determining the best cut speed and stack thickness combination, you already have the perfect “what-if” tool in your arsenal: your CAD/CAM package (we use and recommend IGEMS). You can model different combinations of materials, thickness, and cutting speeds in your CAD/CAM software. It’s a bit of trial and error, but you can use this approach to find the perfect combination for a particular production run. Once satisfied with the solution, confirm it with a small pilot/test run.
Talk to Jet Edge About Cutting Stacked Materials with Your Water Jet System
If you have questions about cutting stacked materials with your water jet, we invite you to give one of our experienced engineers a call. We’ll happily discuss your situation and go over your next steps.
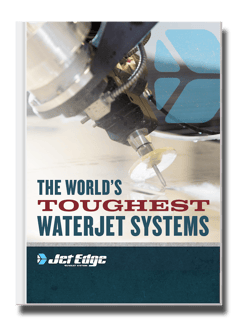
Check Out Our Digital Brochure!
Since 1984, Jet Edge has been designing and manufacturing Ultra-High-Pressure Water jet technology that doesn't back down. Our systems are used around the world in a broad range of industries from the world's leading airlines, to automotive, aerospace and industrial manufacturers, and machine job shops.
To learn more about the Jet Edge difference, our water jet motion systems, pumps and much more, click the button "Download Brochure" to get it now!