When pricing out a part for a customer, there are several variables to consider, such as power and water consumption, material costs, and direct labor. However, depending upon the stock material and your feed rates, garnet often represents the largest operating cost of waterjet cutting tools. So, it makes sense to optimize this indispensable resource. Fortunately, there are best practices for optimizing garnet use. Let’s explore.
The Impacts of Quality Garnet
You get what you pay for, especially when it applies to the garnet you use in your waterjet cutting tools. If you skimp on the quality of the garnet you use, you run the risk of inferior or irregular edge finishes and cut interruptions caused by irregular particle sizes clogging the nozzle. On the other hand, choosing the proper garnet size and quality more than compensates for any cost differential.
Hard Rock or Alluvial - Which is Better?
You have two main types of garnet: hard rock (mined and manufactured) and alluvial (collected and washed). Of these two, the hard rock garnet provides superior results, including:
- Cut denser and tougher materials
- Produce superior edge finishes
- Minimal impurities for minimal reactivity with feed water and stock material
- Reduced wear and tear on equipment
- Lends itself to capture and recycling better
Particle Size and Uniformity
When you purchase a high-quality garnet abrasive, the mesh size you specify is the size you get due to production practices like crushing, refining, and double-sifting. Poor-quality garnet costs less because it’s less expensive to produce and grade. As a result, your abrasive suffers from poor particle uniformity, directly impacting each cut's quality.
Pump Pressure and Waterflow
Another best practice involves optimizing the pump pressure and waterflow rate for each part you cut. For best results, you need to consider pump PSI and horsepower. Here’s what to consider:
- Pump PSI – Generally speaking, the higher the pressure, the faster the cut, with less garnet consumed. However, running a pump at higher pressure increases maintenance costs and may offset abrasive savings.
- Pump Horsepower – Your pump's horsepower determines the total water volume you can provide your waterjet. Higher pump HP creates higher water flow rates, delivering more water and more abrasive. The lower pump HP reduces water volume and usually cutting speeds; however, it may require less garnet to process the part.
Optimize the Garnet Flow Rate
Another best practice involves adjusting the garnet flow rate before and during the cut. While this practice delivers the most benefits when using hard rock garnet, you can also achieve abrasive savings with alluvial garnet. Optimizing the flow rate involves these steps:
- Setting an initial flow rate based on material type, thickness, and cut speed
- Adjusting the flow rate during the cut
- Regular mini hopper calibration
Flow Rate Adjustment
You set a flow rate according to your standard operating procedures before starting a cut. However, the best practice involves watching the cut results and using a Mini Hopper to adjust the flow rate. Incorporating pauses into the cutting program allows you to make flow rate adjustments that minimize abrasive consumption without compromising cut quality.
Calibration
Best practice requires abrasive calibration tests regularly to ensure peak performance and garnet use optimization. Ideally, you should perform an abrasive calibration weekly or after changing the garnet type and size or modifying equipment. If your project involves costly stock, calibration makes sense before starting the cut. Always follow the OEM recommendations for the calibration process.
Master the Science (and Art) of Garnet Recycling
Garnet recycling makes economic and environmental sense and ranks high on our best practices list. How does recycling benefit your operation and the environment? The benefits of garnet recycling include the following:
- Lower wastewater disposal costs and less impact on treatment facilities
- Lower solid waste disposal costs and smaller volumes sent to landfills
- Lower supply water costs when you use reclaimed water and reduced demands on local water supplies
- Longer filter and system seal lifespans through removal of garnet and other contaminants from reclaimed water
Quality garnet is the best candidate for capture and recycling because of particle size uniformity and sharper edges produced during manufacturing. Regardless of starting quality, cutting grains experience edge wear and fracturing during cutting (garnet fragmentation), and so starting with a harder, sharper, uniform product results in better reclaimed abrasive material.
Best practices in abrasive reuse include the following process steps:
- Effectively separate and classify (size) the garnet particles
- Properly clean the recovered abrasive to remove contaminants from the cutting process
- Maintain recycling equipment cleanliness levels
- Keep tabs on equipment efficiency
- Recharge recycled abrasives with new garnet
Recharging your recovered abrasive is the “art” aspect of abrasive recycling. Many variables come into play, starting with the material you are cutting. Over time, experimentation with the percentage of recycled abrasive to new will provide the ideal blend for each material type. A 90/10 ratio (recycled/new) might be perfect for soft materials, while you may need a 10/90 ratio for hard and brittle materials.
Maintenance - A Best Practice Must
It never hurts to underscore the importance of planned routine maintenance for all equipment in machining operations. And, given the precision of waterjet components, maintenance is vital to peak performance.
OEMs always provide maintenance recommendations for their products, and that’s the first place to start. Maintenance recommendations fall into a category we call “predictive.” We test our equipment components to determine the Mean Time Between Failure (MTBF). Based on the MTBF, we develop routine maintenance schedules designed to prevent failures in the first place. We also encourage customers to combine visual and predictive maintenance for maximum uptime and output.
Here’s a general summary of the routine maintenance Jet Edge recommends for its waterjets. Keep in mind that each product has specific requirements.
Weekly: Checks, Cleaning, Adjustment, or Replacement
- Pneumatic filter regulator
- Abrasive flow rate
- Abrasive removal system
- Gas build-up
Monthly: Checks, Cleaning, Adjustment, or Replacement
- Water strainer
- Emergency stops and breakaway head
Yearly Actions
- Grease bearings and slides
- Check and maintain the bellows
- Inspect parts not covered in weekly or monthly checks
Pump Maintenance
- Daily: check for leaks, inlet water pressure, dump valve, and oil levels.
- Weekly: check oil filter pressure and torque of cylinder clamp ring bolts.
- Monthly: Inspect water filters and clean fan filters.
- Half-yearly: Replace the moisture absorption oil filter after 6 months or every 1000 hours of operation.
- Yearly: Replace lubricating oil, filters, and other high-wear items.
So, how does proper maintenance help with optimizing garnet use? Simple. When your waterjet always operates as designed due to proper maintenance, you significantly reduce the factors that can impact (increase) garnet consumption.
The Time to Start Optimizing Garnet Use is Now
With the economic and environmental benefits of optimizing garnet use, there’s no time like the present to start applying the best practices in this article to your waterjet cutting operations. These proactive steps will reduce spending on new abrasives, improve cut efficiency and edge finish, and reduce waste disposal costs.
Talk to Jet Edge About Your Garnet Use
Still have questions about garnet use optimization or any of the best practices we’ve covered? Jet Edge engineers will be happy to take your call and share what we’ve learned so you can become a garnet optimization master, too. Fill out our Contact Form, or call the US toll-free: 1-800-JET-EDGE (538-3343). International callers can reach us at +1-763-497-8700.
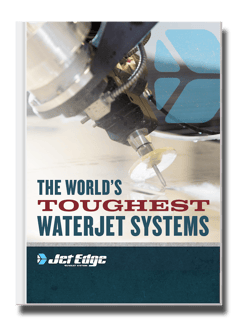
Check Out Our Digital Brochure!
Since 1984, Jet Edge has been designing and manufacturing Ultra-High-Pressure Water jet technology that doesn't back down. Our systems are used around the world in a broad range of industries from the world's leading airlines, to automotive, aerospace and industrial manufacturers, and machine job shops.
To learn more about the Jet Edge difference, our water jet motion systems, pumps and much more, click the button "Download Brochure" to get it now!