Behind every great water jet cutting machine is a high-pressure pump. The pump is the heart of your machine – creating a high-pressure environment that gives life to your cutting head. If you don’t have the right pump, you won’t get the performance you expect. If your pump isn’t reliable, you’ll experience increased maintenance costs and down-time – something that is untenable and unacceptable, especially in larger industrial applications.
If you’re in the market for a new water jet system or have an aging pump, how do you know what type of pump is right for your system, product, and/or application? There are two main categories in which water jet pumps fit: hydraulic intensifier pumps and direct drive pumps (often referred to as crank or positive displacement pumps). How do I know which one if for me?
Hydraulic Intensifier Water Jet Pumps
Hydraulic intensifier water jet pumps, use hydraulic systems to create high-pressure water streams for cutting. Intensifier pumps have several advantages over direct drive machines that often make them a better fit for larger industrial applications.
First, intensifier pumps can operate at higher pressure and have the ability to drive more than one cutting system from a single pump – a huge advantage in larger industrial applications where more than one machine is being used. This greatly reduces upfront capital costs, reduces the footprint of the cutting system, increases the efficiency of your operation, and cuts down on the costs of running two cutters.
Another advantage intensifier pumps have over their direct drive counterparts is longevity and time between maintenance. Due to the way that intensifier pumps use hydraulics to create pressure, there is less wear and tear on the various seals inside the pump system. This results in longer intervals between required maintenance and thus less costs on upkeep. Additionally, the seal replacement is less complicated and can easily be performed by a trained operator or maintenance technician.
The final significant advantage is their ability to maintain a steady, constant pressure no matter what is going on in the various systems they are powering. For example, if a single higher horsepower pump is being used to drive two different cutters at the same time and one machine is shut off, the pressure on the other system will not fluctuate. This works in the reverse as well. In the same scenario if only one cutter is being operated, and then the other is turned on, there will not be any reduction in pressure to the working cutter despite running off the same pump. Hydraulic systems provide extremely stable pressure – something that is often paramount in large industrial applications.
Direct Drive Water Jet Pumps (Positive Displacement Water Jet Pumps)
Direct drive pumps use a crankshaft to move plungers in order to create the pressure that drives cutting systems. Because of the way the direct action creates pressure, these systems tend to be energy efficient as they transfer energy well from the pump to the cutter. However, that comes at a cost as these systems wear faster than intensifier (hydraulic) pumps. This results in shorter maintenance intervals and higher maintenance costs over the life of the pump.
Another limitation of direct drive systems is their inability to drive more than one pump system. Pressure in these systems fluctuate too greatly due to the way pressure is created in a direct drive system making it impossible to power more than a single cutter. Therefore, a dedicated pump is required for each cutting head being driven and in-line pump systems no longer are an option.
Finally, as pressure requirements increase above 65,000 psi, the direct drive pump is no longer an option and an intensifier pump will be required. With the trend toward faster cut speeds and higher production volumes, intensifier pumps rated up to 87,000 psi have been developed and are a great option for larger industrial applications.
However, if you have a smaller application and energy efficiency is a priority, direct drive systems can be a good option. They are generally less expensive up front than their hydraulic counterparts which lessens the barriers to entry, and if production volumes and materials being cut they may be a good option.
What Pump Type is Right for You?
Obviously, selecting the right pump drive technology is just one portion of the analysis required for selecting a pump. There are a series of decisions to be made beginning with what material you are cutting. How much pressure and horsepower are needed? Will I be using abrasive or cutting with straight water? What speed do I want to cut at and what finish level is required?
Make sure your supplier provides a free engineering analysis that includes test cuts designed to determine the most suitable pump and motion system set up for your unique application. In the test cut, a series of tests are completed that define the most efficient speed, horsepower, and cutting pressure to finalize the your throughput requirements.
In practice, larger industrial applications usually select hydraulic intensifier pumps to support higher pressure ratings, multiple heads, and in-line pump systems. Their high-pressure, reliability and longer maintenance intervals make them the most attractive option for these applications.
Smaller operations often use the direct drive pumps due to the lower entry costs and lighter duty requirements.
For more information on Selecting the Right Ultra-High Pressure Water Jet Pump, visit https://www.azom.com/article.aspx?ArticleID=13631
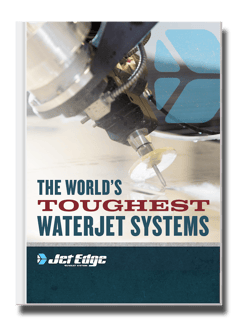
Check Out Our Digital Brochure!
Since 1984, Jet Edge has been designing and manufacturing Ultra-High-Pressure Water jet technology that doesn't back down. Our systems are used around the world in a broad range of industries from the world's leading airlines, to automotive, aerospace and industrial manufacturers, and machine job shops.
To learn more about the Jet Edge difference, our water jet motion systems, pumps and much more, click the button "Download Brochure" to get it now!