Water, the power behind water jet cutting systems, serves two primary purposes: processing and cooling.
Process Water
Process water is the water that is supplied to the high-pressure pump and used by the cutting head to cut the material. This inlet water comes directly from the tap or from a water treatment system such as a reverse osmosis system.
Cooling Water
Cooling water is introduced into the hydraulic loop via a heat exchanger and is used to cool the hydraulic fluid in the pump system.
This blog will focus on Process Water and how to minimize waste.
Key Water Considerations for Your Process Water
In some regions, water supply is taken for granted. In others, not so much. Additionally, to keep your CNC water jet cutter and ultra-high pressure pump performing at its peak, the water needs to be maintained at a core temperature.
Do I Have a Reliable Water Supply?
Reliable, as we use it in this context, means having confidence that you will have enough water from your supply source to run your water jet system without interruption. Water use restrictions directly affect the "reliability" of your water supply by imposing usage limits and/or high utility costs from your municipal water utility.
Water use restrictions are an increasingly common issue in parts of the United States, hit by severe and prolonged droughts. The following graphic from the National Oceanic and Atmospheric Agency (NOAA) U.S. Drought Monitor System illustrates the extent of drought areas as of November 8, 2022. Locations with the darkest red already have restrictions, and other regions are actively considering the need.
Open Loop Water Jet Systems vs Closed Loop Water Jet Systems
Open Loop Systems for Process Water
Let's face it, your water jet cutting system requires a large amount of water. Most systems rely on a continuous incoming water stream flowing through the cutting head to make cuts. The added Process Water flows into the catcher tank and is drained off via an overflow drain, hence, an “Open Loop System”. Many companies, if not most, just discharge the excess water directly into the city sewage or drainage system. These Open-Loop Systems incur higher utility costs but avoid the capital cost of water recycling.
Closed Loop Systems for Process Water
Conversely, closed-loop systems, often referred to as Closed Loop Filtration Systems or Closed Loop Water jet Recycling Systems, reduce total water consumption by recirculating the Process Water rather than continually discharging it to a drain. If abrasive cutting is performed, an abrasive removal system is added to the system, collecting the spent garnet and filtering the process water before returning it to the high pressure pump. Recycling water is both an environmental decision and a compliance decision in areas with water use restrictions. See our blog on disposing of spent garnet to learn more about managing spent abrasive.
How Do Closed-Loop Process Water Systems Work?
The following diagram illustrates the Closed Loop Water Recycling System in a typical abrasive water jet application. The high pressure intensifier pump delivers the process water to a cutting head above the catch tank. An abrasive hopper stores the bulk garnet, delivering it to a metered hopper mounted on the gantry. The process water, spent garnet and small material drops are captured by the catch tank as the abrasive water jet cutting occurs.
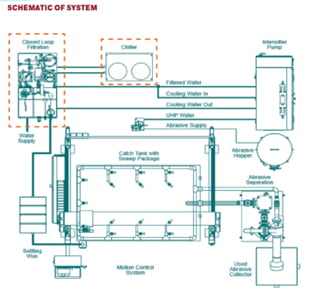
The catch tank incorporates a sweeper package, which pulls the heavier, suspended garnet and small material drops in the tank to an abrasive collector via an abrasive separator pump. The used abrasive is captured in a sack for removal and the filtered water is returned to the catcher tank.
Additionally, water is pulled from the top of the catcher tank into a settling weir for further filtering, prior to delivering it to the closed loop filtration system. The Closed Loop Filtration system will again filter the water and deliver it to an inline chiller that will to bring it back to 70o F. The chilled water will be returned to the high pressure pump, beginning the the cycle again.
When Should You Use a Closed-Loop System?
Open-loop water jet systems benefit from their simplicity and usually the incoming Process Water remains at temperatures within recommendations and does not require additional cooling. Closed loop systems will be preferred when:
- A fresh water supply or drainage method is not readily available where the equipment is located in the facility.
- The utility costs of the incoming water supply outweigh the costs of adding a water filtration system and closed loop chiller.
- Local regulators require it due to the environmental concerns of either the volume of water being consumed or what is being discharged into the drainage system.
- Environmental concern and stewardship are a priority cultural value of the user.
Environmental Water Use and Water Management Regulations
As mentioned, environmental agencies are regulating water use more strictly, especially in drought-impacted areas. Restrictions on the amount of water used represent the most common approach to managing the water resource. Environmental agencies also regulate water discharge by volume and the content of the discharged water. In both cases, closed-loop systems offer a superior solution by managing input and discharge water volumes.
Talk to Jet Edge About the Benefits of Closed-Loop Systems
The benefits of closed-loop water jet systems are substantial and represent the best practice for water jet cutting. However, they can increase the upfront system costs and complexity of your water jet cutting system.
Talk with a Jet Edge expert who can help you engineer the closed-loop system that matches your unique needs and read these excellent blog topics on related subjects:
- ALL ABOUT WATER JET CHILLERS AND CHILLING SYSTEMS
- CAN SPENT GARNET BE RECYCLED?
- WHAT IS ABRASIVE REMOVAL?
- WATER QUALITY AND WATER JET FILTER REPLACEMENT BEST PRACTICES
- HOW DOES YOUR WATER QUALITY IMPACT YOUR WATER JET CUTTING?
Additional Resources at Jet Edge
We strive to publish as much information as possible to enable our customers to make the best decision for their specific water jet cutting needs. Our Guide to JetEdgeWaterjets.com provides tips to get the most out our website on motion systems, high pressure pumps and accessories. Our Case Studies, water jet cutting technology and best practice Blog Library provide tips on best practice and how other approached water jet cutting in their visit. Visit our Resource Center for all things water jet!
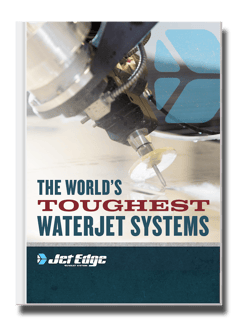
Check Out Our Digital Brochure!
Since 1984, Jet Edge has been designing and manufacturing Ultra-High-Pressure Water jet technology that doesn't back down. Our systems are used around the world in a broad range of industries from the world's leading airlines, to automotive, aerospace and industrial manufacturers, and machine job shops.
To learn more about the Jet Edge difference, our water jet motion systems, pumps and much more, click the button "Download Brochure" to get it now!