To state the obvious, water is really an important element of water jet cutting and processing. We encourage you to read our water quality post to learn more on the topic of water quality and how that quality is measured.
Water serves two primary purposes in your water jet cutting system: processing and cooling. But did you know, the water in both of those processes has a temperature standard it should meet so your system performs at its highest level? “Out-of-spec” water temperature will eventually affect cut quality and edge finish and will reduce seal, pump, and filter lifespans.
Water Types
Process Water
Process water is the water that is supplied to the high-pressure pump and used by the cutting head to cut the material. This inlet water comes directly from the tap or from a water treatment system such as a reverse osmosis system. The inlet water temp should not exceed 70F.
Cooling Water
Cooling water is introduced into the hydraulic loop via a heat exchanger and is used to cool the hydraulic fluid in the pump system. Hydraulic fluid temperature should be maintained at a temperature not greater than 120F.
What's Your Delta-T?
The difference between your water supply temperature and the recommended maximum of 70o F determines your temperature differential or delta-t.
The temperature of groundwater varies widely with geographic location, ranging from 35o to 77o F, as shown below and determines the temperature of your incoming water supply, whether it comes from a water utility or a well. The good news is that most areas in the lower 48 States enjoy standard tap water temperatures well below 70o F and can be used as process water pre-cooling.
Source: eno scientific
If you'd like to get groundwater temperatures in your area, this interactive map on Hydro Flow's website will help. This knowledge is useful for planning, but always use a temperature gauge to display the real-time temperature of your supply water.
Using water warmer than 70o F directly affects pump performance, pump seal lifespan, and eventually cutting performance, including accuracy and finish. None of these impacts are beneficial to your ROI, so it's prudent to understand how chillers impact process water and cooling water.
Managing Process Water in a Water Jet System
Open-Loop Water Systems - Process Water
Open-loop systems provide the high-pressure pump with a continual supply of fresh water. The additional water flow, spent Garnet if abrasive cutting, and small material drops, fall into the catcher tank. Unless the new water is discharged to a drain, the tank will overflow. Whether you are cutting with water alone or with abrasive, the overflow is usually discharged directly into a drain. However, certain materials, as determined by your local codes and ordinances, will be deemed hazardous and must not be drained off. See our Blog on disposing of Spent Garnet to learn more.
The primary benefit of an open-loop system lies in its simplicity. You can view an open loop system as having three distinct stages:
- Input supply water flows to the high-pressure pump.
- The water jet uses pressurized water for cutting.
- The spent water flows directly to the drain.
Since the Open-loop systems always have an incoming water stream, they generally do not require pre-cooling and avoids the cost of chilling equipment and its operating expenses. However, during certain times of the year as ambient temperature increases driving water temperatures above 70o F, the incoming water temperature may require chilling.
Open-loop systems inherently require a higher water supply and incur the associated utility costs. The utility costs will vary depending upon water availability. Your local authority may impose restrictions on water usage and will regulate discharge water. If your water supply contains high concentrations of dissolved and suspended solids, or materials deemed hazardous, an open loop system may not be an option. So, what is my alternative? A Closed-Loop Water System is the solution.
Closed-Loop Water Recycling Systems - Process Water
The closed-loop system, often referred to as a Closed Loop Filtration System, recycles the process water rather than continually discharging it to a drain thereby reducing total water consumption. If abrasive cutting is performed, a spent garnet collection/filtering system is also integrated into the closed loop system. Recycling water is both an environmental decision and a compliance decision in areas with water use restrictions.
The friction that results from the water jet cutting process, will warm the water that is discharged into the tank. Since the water is recycled into the system its temperatures will rise. The recycled water must be cooled back to the specified 70o F operating temperature before it reaches the high-pressure pump. To achieve the temperature reduction, an in-line Chiller is inserted into the system. The cost of a chiller and the filtering system for the process water replaces the utilities cost of the incoming water and dumping expenses when weighing an ROI for this investment.
Cooling Water and Chilling for Intensifier Pumps
Hydraulic Intensifier Pump Requirements - Cooling Water
Hydraulic intensifier pumps are the most common type of pump used in water jet cutting. This type of pump uses hydraulic fluid that has a specific operating temperature range. The second use of water in water jet cutting systems is for cooling the high pressure pump’s hydraulic system. When hydraulic fluid heats up, it becomes "thinner," losing viscosity, its lubricating ability and becomes less efficient. The higher temperatures will also decrease the life of consumables, such as seals and high pressure hoses, and lead to higher maintenance costs. To counter this effect, Hydraulic fluid temperatures should be maintained at 120o F or below.
The most common solution to keeping your hydraulic fluid at temperature involves utilizing a heat exchanger in the hydraulic cooling loop of your pump. The purpose of the heat exchanger is to transfer the heat from the hydraulic oil to the cooler process water to regulate temperatures.
When the heat exchanger alone is not adequate to keep the hydraulic fluid at 120o F, or if the usage of incoming cooling water is very high, a High Pressure Pump Chiller is added specifically to cool the hydraulic system. Cooling water from the chiller, mixed with Glycol to increase heat absorption, is pumped through the cooling loop to transfer the heat from the hydraulic fluid, keeping it within the proper temperature range. The heated water from the intensifier pump is returned to the chiller to be cooled and recirculated again through the heat exchanger.
The Most Common Types of Water Jet Chillers
There are three common types of water jet chillers, each having their unique purpose: in-line chillers, high-pressure recirculating pump chillers, and flow-through chillers.
In-Line Chillers
The in-line chiller, for use in closed loop systems, sits between the equipment that removes abrasives, spent material and other debris and the high-pressure pump feeding the cutting head. The filtered water is chilled and sent back to the high pressure pump to be used as process water.
A major benefit of these chillers is that they remove the waste heat for use with both your process and cooling water. Besides eliminating the cost of dedicated systems for each water use, in-line chillers significantly improve the maintenance intervals on your pumps, keeping them performing at maximum levels during lengthy cuts.
Application: Used exclusively with closed-loop systems.
High-Pressure Pump Chillers
This dedicated chiller cools down the water used to keep the high-pressure pump's hydraulic systems within the proper operating temperature range, less than 120o C. Using Glycol as the cooling agent, this dedicated, system continuously chills the water cooling the hydraulics of the high-pressure pump.
The continuous supply of cool water to the high-pressure pump hydraulics improves pump performance and maximizes seal life. In addition, pump chillers are available in a range of sizes, simplifying the task of picking the best chiller size for your pump and environment.
Application: Open-loop systems where the cooling water does not lower the hydraulic fluid operating temperature to required range.
Flow-Through Chillers
These chillers cool the process water before it enters the high-pressure pumping system, ensuring the cutting process always has water at the proper temperature.
This cooling solution rapidly cools the incoming water in a single pass. Since they operate on the pressure of the process water they're cooling, they do not require pumps of their own to move the water forward. Keep in mind that once the process water goes through the cutting stage, it may still require chilling.
Application: For use with direct drive style high-pressure pumps in an open loop system.
Talk to Jet Edge!
Jet Edge offers a full line of ultra-high pressure intensifier pumps that power its world class water jet systems. For performance you can count on every day, our HERO Series of water jet pumps leads the way. If you would like a little help in building your system profile, our 4-Step Buying Guide might be a good place to start.
Since 1984, Jet Edge has been designing and manufacturing ultra-high pressure water jet technology that doesn’t back down!
Contact us today to learn more about Water jet Cutting or visit our extensive Blog Library located in our Resource Center at JetEdgeWaterjets.com. You can also reach us by phone toll-free at 1-800-JET-EDGE (538-3343) or internationally at +1-763-497-8700.
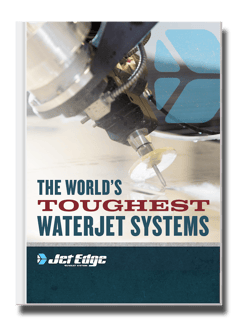
Check Out Our Digital Brochure!
Since 1984, Jet Edge has been designing and manufacturing Ultra-High-Pressure Water jet technology that doesn't back down. Our systems are used around the world in a broad range of industries from the world's leading airlines, to automotive, aerospace and industrial manufacturers, and machine job shops.
To learn more about the Jet Edge difference, our water jet motion systems, pumps and much more, click the button "Download Brochure" to get it now!