Lasers (Light Amplification by Stimulated Emission of Radiation) are a popular cutting technology within the metal fabrication industry. To oversimplify, the laser cutting process uses a beam of amplified light to rapidly melt a cut line through materials creating the cut in a process referred to as “thermal separation”. Fiber lasers, as opposed to C02 and YAG lasers, are increasingly becoming the preferred technology in the metals industry due to their wide power range, consistent beam quality, and range of materials they are capable of cutting. These cutting tools are fast, offer excellent precision and the most powerful ones may cut dense materials like stainless steel up to .5 inches.
In contrast, water jet machines cut using ultra-high-pressure water delivered through precision orifices and nozzles to a cutting head. This pressurized water is then directed towards the material that needs to be cut. Many materials may be cut with water only but when you add an abrasive, a whole array of dense specialty materials including titanium, stainless steel and Inconel’s can be water jetted.
Thermal Separation Limitations
The heat generated by Thermal Separation (the cutting method of lasers), while intense has limitations. Material types that reflect, are combustible, have low melting points, or are very thick do not react well to the heat. Both laser cutting and plasma cutting, have similar challenges due to the heat generated and have narrower ranges of operation. Accordingly, laser cutters are primarily used to cut processed metals such as mild steel, stainless steel and aluminum, however, they are limited to cutting materials less than one inch (<1”) thick. Specialty metals are less likely to be cut with lasers or plasma as the heat alters the material properties and often requires additional processing. The area adjacent to the cut is known as the heat affected zone, or “HAZ”.
Softer materials, composites, fabrics, plastics, and foam cannot be cut with lasers because of the damage created with the intense heat.
How Do Lasers Stack Up to Water Jet as Cutting Systems?
While there is some overlap between what can be done on a CNC Water Jet and a Laser, there are many differences that need to be compared to determine which system is right for you. Let’s examine the most distinguishing differences, starting with cut quality.
Cut Finish Quality
When edge quality matters either for the elimination of secondary operations or just for the aesthetics, no machine tool beats a water jet. Measured across five levels of quality, Q1 being the highest and Q5 the lowest, waterjets may be adjusted to eliminate striations on the edge creating a first-cut finish that meets the final specifications. And, since water jet machines cut without creating dross or splatter, additional surface cleaning such as grinding is unnecessary.
Cut Complexity
Lasers are limited to vertical 90o cuts in the X and Y planes due to the nature of the cutting process. By comparison, 5-axis water jet machines can perform complex cuts and bevels accurately on flat or contoured shapes. This capability allows users to cut a wider range of components on a single machine, eliminating the need to completely fabricate and finish a part on multiple machines.
No HAZ
Cutting tools that use or generate heat can create heat-affected zones or HAZ’s. HAZ’s are an issue because they negatively affect the material on either side of the cut. It can damage or remove tempering, deform, or warp the material, create brittleness, damage finishes and coatings, create oxidation around the cut, and so on. The result is increased post-cut work to fix the HAZ effects. Water jets are “cold-cutting” tools and never create a HAZ.
Cut Precision
This is a toss-up with each capable of cutting near net shapes. Laser cutting tolerances range from +/- 0.001-0.005”. Water jet machines commonly have tolerances around +/- 0.005”.
Maintenance
Both systems require regular maintenance to operate at 100% quality and capacity. Laser maintenance requirements depend upon the technology used (gas, solid-state, chemical, semiconductor, etc.). In water jet systems, the type and power of the pumps have a bearing on maintenance requirements. Both systems use consumables; nozzles, filters, and abrasives top the list for water jets, and for lasers, gas and lenses.
Material Compatibility
Lasers' thermal separation cutting process limits the range of materials to metals less than an inch thick. Water jet machines can cut astounding material thicknesses such as 20” thick aluminum block and 6” thick stainless steel. Waterjets are also nearly material type “agnostic.”. Just some of the materials a water jet can cut include:
- Food
- Foam
- Fabrics
- Metals
- Specialty Alloys
- Stone
- Ceramics
- (see our blog Yeah, you can cut that with Water Jet Machines for a more complete list.)
Cut Speed
Lasers win hands down when it comes to cutting speed in 2 dimensional, thinner gauge metals.
Total Cost of Ownership (TCO)
High end fiber laser systems can reach seven figures depending upon size and speed. A fully loaded water cutting system may reach half that number. However, both systems have lower cost, lower featured and lighter duty models at very affordable costs for entry level users.
There are maintenance and operating costs for both technologies, with lasers typically having lower consumable costs post installation. To get a clearer picture of operating costs, you’ll want to ask your manufacturer about the per-hour run times of their machines, as these vary significantly from system to system and by configuration based on production volumes.
Since water jets cut a more expansive range of materials, can cut a broader array of shapes and excel in reduced post-cut processing they may deliver a higher ROI depending upon volumes. These characteristics often tip the TCO scales in favor of water jets.
Laser Cutting vs. High-Pressure Water Jet Metal Cutting - Which is Better?
In conclusion, while lasers generally cut faster and offer exceptionally narrow kerfs they are limited to a much narrower range of metals and shapes. In contrast, water jets are a much more versatile tool, allowing you to process virtually any material, producing high quality edge finishes, and execute complex 5-axis cuts on one system. In high volume metal shops, it is usual to have both machine tools dedicated to the production they are best suited for.
This is Complex. We Get It - We're Here to Help
Jet Edge has done hundreds of installations and can walk you through each of these and other methods to enhance your productivity. We also strive to publish as much information as possible to enable our customers to make the best decision for their specific needs, so visit our Blog Library located in our Resource Center to read about all things water jet. Additionally, have a look at our Case Studies and learn how others have managed through the selection process.
Visit our website to learn how to get the most out of https://jetedgewaterjets.com/jetedgewaterjets-com-site-navigation-resources/
Click above to learn how to get the most out of our website, JetEdgeWaterjets.com
Talk to Jet Edge
Contact us today to learn how to increase your service offering to your customers. You can also reach us by phone toll-free at 1-800-JET-EDGE (538-3343) or internationally at +1-763-497-8700.
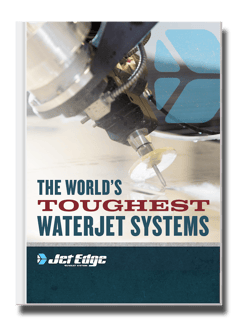
Check Out Our Digital Brochure!
Since 1984, Jet Edge has been designing and manufacturing Ultra-High-Pressure Water jet technology that doesn't back down. Our systems are used around the world in a broad range of industries from the world's leading airlines, to automotive, aerospace and industrial manufacturers, and machine job shops.
To learn more about the Jet Edge difference, our water jet motion systems, pumps and much more, click the button "Download Brochure" to get it now!