If you’re in the market for a new or used water jet cutting system, then we don’t have to tell you how expensive these machines are. Water jet cutting systems are complex machines with high powered pumps, automated cutting heads, lots of moving parts, and optional add-ons – all of which contribute to the expensive nature of the machines.
However, the costs of any one system can vary greatly when compared to another. Depending on a variety of factors ranging all the way from pump type and pressure to what kind of table and cutting head system, the cost differences between any two systems can be tens of thousands of dollars. What specific factors impact price the most? How is the cost of your system calculated? In this post, we’ll explore the factors that have the greatest impact on the cost of any one system.
Pumps and Horsepower
What kind of a pump you need all depends on your product and/or application. However, the various attributes of the pump required can have a large impact on the price of the pump and thus the overall system. Generally speaking, the more horsepower you need the pump in your system to have, the higher the cost. The type of cutting system you’re using (and the various parts of the system) impact what horsepower rating pump you’ll need.
To calculate the amount of horsepower you need. Contact your distributor, supplier and/or manufacturer. This tends to be a complicated issue, so we feel it’s best to talk it out with a professional.
Cutting Head and Axis
Again, like most cutting system attributes that factor into the total system costs, cutting head and axis type really depend on your product and/or application. However, the type of cutting head and axis requirements needed for your cut will greatly impact the price of the cutting system.
For basic cuts involving simple edges and materials, a 3-axis system will likely suffice. However, for more complex cuts where greater movement capabilities are needed, a 5-axis cutting head may be required. 5-axis systems are more expensive; however, they offer much greater flexibility in terms of the types of cuts they can perform.
For applications where you want to cut the same part multiple times the addition of a spreader bar with more cutting heads can greatly increase the efficiency of the machine but with the added cost of course.
Abrasive Water Jet Systems vs Water-Only Systems
Stop us if you’ve heard this before, but the need for an abrasive-capable water jet cutting system is usually dictated by your product and/or application. Adding abrasive capabilities to your system significantly increases the cutting power of a water jet system. However, it also significantly increases the complexity of it. It does this is several ways:
- Adding the need for an abrasive hopper to store the abrasive during cutting
- Additional tubing from the hopper to the cutting head is required for smooth delivery of abrasive
- Pump chillers can extend the life of the pump and cutting system including those that use abrasives
- Using as abrasive removal system significantly reduces downtime and catch tank maintenance
With the additional system components and complexity comes increased costs. Abrasive systems are more expensive out-of-the-box with the total system costs increasing as you add optional components (like environmental systems, etc.).
Table Size and Length
When it comes to table size/length of the table and possible custom configurations, there is a pretty simple rule: the bigger the table, the higher the costs. Beyond that consideration, if custom table sizes are required for your product and/or application, that will generally increase the total cost of your system as well.
Environmental Systems and Other Add-Ons
As mentioned above when discussing the additional costs associated with abrasive systems, there are other add-ons that can increase the overall cost of your system. One such example is a closed-loop recycling system. These systems are very effective at mitigating environmental issues related to mixing abrasives with water. With a closed loop system you eliminate the need for a drain by filtering out the used abrasive and cleaning the water before it is sent to a chiller to cool the water before sending it back to the high pressure pump. This saves on water usage and sewage costs.
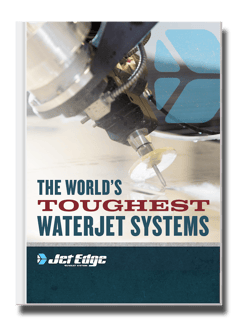
Check Out Our Digital Brochure!
Since 1984, Jet Edge has been designing and manufacturing Ultra-High-Pressure Water jet technology that doesn't back down. Our systems are used around the world in a broad range of industries from the world's leading airlines, to automotive, aerospace and industrial manufacturers, and machine job shops.
To learn more about the Jet Edge difference, our water jet motion systems, pumps and much more, click the button "Download Brochure" to get it now!