The objective of surface detection is simple: maintain the required standoff distance (SOD) between the cutting head nozzle tip and the stock’s surface across the entire cut path - regardless of material flatness and surface irregularities. The cutting surface of most materials will vary as they are not yet machined to ensure perfectly level surfaces.
The reasons why controlling the SOD is important are also simple: If the cutting head maintains a flat path and doesn’t account for surface variations, the SOD will vary across the cutting surface. As a result, cut quality will be impacted as the width and pressure of the water at the point of contact changes as the surface distance changes. When you are machining material to tighter tolerances, this variation is unacceptable and surface detection becomes required.
With water jet systems, there are two main surface detection approaches to controlling SOD: contact and non-contact, both of which have their pros and cons. For this article, we will look at contact surface detection using probes that continually monitor the SOD. To learn about non-contact laser mapping check out our previous post by clicking here.
Now let’s explore contact surface detection.
Why is SOD Critical to Water Jet Cutting?
The optimal SOD depends on the type of cutting being performed, the material being cut, and the desired cut quality. As a starting point, the optimum SOD guidelines for the highest cut quality suggest:
- 3-axis abrasive systems SOD: 0.125” - 0.250”.
- 5-axis abrasive systems SOD: 0.125”
To ensure a consistent cut finish through the entire cut cycle, the SOD should be consistent at each point along the cut path, adjusted to account for surface irregularities. It’s hard to overstate the importance of maintaining an optimal SOD in high-precision and/or complex cuts. Several undesirable things can result when the machine doesn’t maintain a consistent SOD such as:
- Cutting too close to the material can cause back pressure, which can clog the abrasive line, damage the nozzle, and/or result in the loss of the assembly
- The nozzle can contact the material being cut, damaging it or other parts of the water jet.
- An SOD that is too high can cause dimensional problems as the spray pattern enlarges and the delivered cutting pressure is reduced as a result of the larger distance from the material
In all of these cases costs increase and productivity drops. That’s two more reasons why it makes sense to mitigate these issues using surface detection systems with your water jet cutter.
Contact Height Sensor Operation
As the name implies, contact height sensors are designed to remain in contact with the surface of the material during cutting. The sensor sends a continuous data stream to your system controller via a position transducer.
Whenever the sensor detects a surface irregularity due to a change in probe height, the transducer converts this mechanical height data to a form of data the controller can interpret. When an irregularity greater than 0.040 inches (1 mm) is sensed, the controller immediately adjusts the cutting head height to compensate and maintain the programmed SOD. This creates a constant feedback loop that keeps your cut consistent throughout the program.
Contact height sensors utilize a probe foot that contacts the work piece around the cutting head nozzle. By attaching at this point the height data is collected from a point as close as possible to the cut location. They are attached to the cutting head using a holder or bracket. This way they maintain the SOD even during rapid cutting movements.
Shown above on the left is a 3-axis contact height sensor and on the right a 5-axis contact sensor
Advantages of Contact Height Sensors
Automatic real-time compensation for surface height fluctuations is the main advantage of contact height sensors. Because they are in constant physical contact with the stock surface, variations and irregularities are immediately accounted for. This results in the most consistent cut finish, kerf and dimensional tolerances, taper quality, and cut speed.
When equipped with feature avoidance capability, the contact height sensor is prevented from passing over a previously cut part which can spring or tip up after being cut. This protects the cutting head from colliding with these parts, avoiding damage to the cutting head, sensor, and workpiece.
Used in conjunction with lights-out cutting, the cutting will pause immediately in the event of contact with a fixture or part.
Should the probe come into contact with the material edge, it will automatically shut the cutting down until an operator corrects the material position. This further reduces the risk of damaging the cutting head or production part.
The contact height sensor can be used in 3-axis, 5-axis, mid-rail, and high-rail applications thus making it a versatile addition to your water jet cutting toolkit.
Multiple sensors can be used with dual carriage mid-rail systems, which can have two (2) sensors, and multi carriage high-rail systems, which can have up to four (4) contact height sensor assemblies mounted on individual sub-Z cutting tools.
The Limitations of Contact Height Sensors
Considering that every technology has some limitations, it’s important to point out some considerations with contact height sensors.
- Because the sensor is in physical contact with the stock with a force of 32 oz (0.9 kg), damage to delicate materials and deformation in thinner stock are possible. In both situations, cut and finish quality may be impacted.
- Since the sensor is mechanical, it requires more maintenance over time than their laser mapping alternatives due to wear and tear and possible probe foot replacement should it come in contact with a fixture or sprung part.
- The contact height sensor must be calibrated whenever it has been disabled, when an emergency stop is initiated, or whenever the system controller power is turned off. It also must be recalibrated to change the standoff distance of the nozzle or to change nozzle lengths.
Choosing the Right Surface Detection Method
What surface detection is the best fit for your application? Hopefully the following table can help narrow your focus:
Criteria |
Contact SOD Control |
Non-Contact Laser SOD Control |
Best for Material Types |
Thicker, sheet materials; materials subject to spring relief during the cut |
Highly irregular, or non-flat materials; materials that do not deform during cut |
Cut Complexity |
Ideal for simpler, lower-complexity cuts on 3-axis systems; low contoured 5-axis cutting from plate |
Best for advanced 5-axis systems with higher-precision needs |
Dynamic Adjustment |
SOD adjustment is made in real time as material shape changes |
SOD adjustments are not dynamically made after the cut begins |
Surface Characteristics |
Gradual gradient surface variations are preferred; surfaces that will not be damaged due to contact with the probe foot |
Works best with shapes and surfaces that allow uninterrupted laser reflection; material would be damaged by pressure foot |
Impact on Cut Speed |
Often a slower federate is used due to the physical contact of probe |
No impact on cut speed as SOD is programmed into file |
Risk of Interference |
Hold down clamps/ fixtures in the cut path may be hit and cause damage. |
Changes to the hold down method post scan, parts that have tipped and material that springs during the cut will not be detected |
Maintenance |
Higher mechanical maintenance on foot due to wear from contact; requires occasional recalibration per above |
Laser must be kept clean and stored securely in its enclosure during cut |
Cost |
Lower upfront cost but some ongoing maintenance costs over time |
Higher initial investment but potentially greater efficiency |
Talk to Jet Edge About Surface Detection Solutions
Maintaining a precise SOD during the cutting and machining process is vital to producing consistent edge finishes and cut accuracy through the entire cut. Using surface detection methods, you also can avoid the damage associated with coming into contact with material or fixtures during the cut. Jet Edge’s water jet cutting systems contribute to your bottom line by improving productivity and reducing scrap loss.
If your water jet system isn’t currently using surface height detection, we encourage you to investigate how it can help your operations today. Jet Edge’s engineers are capable and ready to speak with you and help select the best solution for your application.
Visit our Blog Library and Comprehensive Video Collection
Jet Edge offers a comprehensive library of maintenance training videos, case studies, best practice blogs and a whole lot more in our resource center.
If you would like to learn more about Jet Edge Water jet Systems, visit us online at jetedgewaterjets.com. If you are ready to speak with your regional expert, just let us know on our contact us page, or call us toll-free at 1-800-JET-EDGE (538-3343), internationally at +1-763-497-8700.
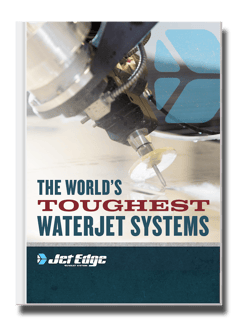
Check Out Our Digital Brochure!
Since 1984, Jet Edge has been designing and manufacturing Ultra-High-Pressure Water jet technology that doesn't back down. Our systems are used around the world in a broad range of industries from the world's leading airlines, to automotive, aerospace and industrial manufacturers, and machine job shops.
To learn more about the Jet Edge difference, our water jet motion systems, pumps and much more, click the button "Download Brochure" to get it now!