If you’re in an industry using water jet cutting machines you know how important proper machine maintenance is. You know that up-time is crucial to productivity and profitability and how devastating downtime can be. This is especially true with water jet cutters using garnet abrasives.
Using abrasives with your water jet cutter adds to the complexity of your system and thus increases your risk for a breakdown and the subsequent downtime. Clogs are one of the most common causes of downtime for water jet cutters using abrasives. However, with proper precautions and maintenance, you can significantly reduce your chances of an abrasive clog in your cutter – keeping your machine cutting longer between regular maintenance intervals. Here are 9 things you can do to prevent abrasive clogs:
The 9 Steps to Preventing Abrasive Clogs
-
Use Quality Abrasive from a Reputable Source
Abrasives grades are distinguished by hardness, particle density, particle shape, purity and consistency. The higher the grade, the more expensive the abrasive. The use of poor-quality abrasives is one of the leading causes of abrasive water jet clogs. Cheaper abrasives do not perform at the same manufacturing standards of higher-quality abrasives and the inconsistency of the product can introduce contaminants that will clog your machine.
Take the time to understand how to choose the right garnet type for your specific cutting and buy your garnet from a reputable source. Make sure they are high quality products before dumping them in your cutter’s hopper.
-
Keep Abrasives Dry at All Times
Humidity is your enemy! Don’t allow your abrasives to be exposed to high humidity for extended periods of time. A high moisture content in your abrasive will restrict flow and make it harder for your machines feeding system to deliver a consistent stream to the cutting head. Make sure you always store your garnet abrasives in a cool dry place when not in use. If your garnet does come in contact with water, allow the abrasives to dry completely before using or simply dispose of it properly.
-
Take Precautions to Prevent Debris from Entering the Hopper
A bulk abrasive hopper uses air pressure to deliver the garnet to the cutting head via abrasive lines. High quality abrasives will do no good if during the process of loading the bulk hopper packaging debris and other contaminants make it into your mix. Even small foreign debris from the packaging can enter the abrasive line and clog your machine. Take precautions when loading your hopper to ensure no other items make it into your mixture and always use the screen.
-
Ensure Your Abrasive Feed Rate Matches Orifice and Nozzle Size
The bulk abrasive hopper delivers abrasive to a variable aperture mini hopper that meters the flow of abrasive delivered to the cutting head. The cutting head utilizes an orifice that focuses the water stream delivered by the ultra high-pressure intensifier pump into a fine stream for cutting. The orifice is specified by jewel material type, (sapphire, ruby, synthetic and diamond are the most common materials) and by its inside diameter. The I.D. dictates the volume of water and abrasive that can be delivered to the nozzle. Clogs happen when the abrasive feed rate set at the metering hopper, exceeds the rate at which your orifice and nozzle can consume the abrasive. The correct feed rate changes when garnet types and orifice sizes are changed. Before you start cutting, make sure that the abrasive feed rate set at the mini hopper does not deliver more abrasive to the cutting head than the orifice and nozzle size used can accommodate. Performing an abrasive weigh test is the best way to accurately “recalibrate” the dial settings.
-
Use the Right Orifice/Nozzle Combination
The orifice and nozzle combination work together and will dictate actual water pressure and flow to the cutting head, which in turn dictates the cutting rates and cut quality your water jet system produces. Similar to orifices, nozzles are rated by the material quality and process used to manufacture them, their I.D. and by their length. A larger ID allows for greater water and abrasive flow and generally provides for a faster cut. A general rule of thumb is getting an ID that is three times larger than the orifice ID. When the proper combination of water flow, water pressure, orifice size and nozzle is not achieved, clogs can occur. Additionally, match the timing between the delivery of the water stream and the abrasive stream. Keeping the abrasive preload light, especially when piercing, improves the cutting. Talk to your manufacturer to make sure you have the correct orifice/nozzle combination before cutting.
-
Maintain a Proper Standoff
5-axis abrasive cutting requires the tip of the nozzle to be approximately .125” from the material surface. With 3-axis abrasive cutting that range may vary from .125” to .250” inches. Cutting too close to the work surface, or actually touching the work surface with the nozzle, may create back pressure. When this happens, the back pressure prevents the flow of abrasive and will actually cause the abrasive to get wet with the moisture back tracking up your abrasive line causing an instant clog. Keep the correct distance from the nozzle to the material being cut to avoid this. Jet Edge systems utilize a relief valve that incorporates a flap that opens to discharge water/abrasive slurry that flows up the delivery tube toward the mini hopper should the abrasive nozzle become blocked. This ensures the abrasive in the mini hopper remains dry.
-
Replace Worn Orifices
Nozzles will tend to wear in an hourglass shape and the larger opening at the top may produce “packing”. Monitor operating time on orifices and nozzles and replace them as soon as you see cut accuracy and finish deteriorating.
-
Check and Maintain Your Abrasive Feed Lines
Garnet is abrasive by definition and over time all parts that come in contact with it will wear. Check the abrasive feed line from the bulk hopper regularly to confirm enough flow is being delivered to the metering hopper and change it out at scheduled maintenance intervals. Over time excessive wear or a buildup of static electricity, especially in arid regions, may be generated and inhibit flow. Replace abrasive feed tubing, abrasive inlets and other parts that come into contact with the abrasive at regular scheduled intervals and you’ll reduce or prevent longer downtime in the future.
-
Know Your Water Jet Manual
It goes without saying but knowing your machine’s operating manual inside and out can prevent a lot of issues during cutting. Your manual will detail recommended maintenance intervals and specify required parts and components. Post daily routine maintenance at the workstation to remind operators. Monitor cut hours on wear parts. Schedule preventive maintenance before your system goes down to ensure there is minimal disruption to production time.
Visit Jet Edge’s MyEquipment page to learn how you can have your manuals posted online and linked to our E-commerce store so you never have to guess again what parts you need for your system. Take the time to know your individual machine’s manual and you will be rewarded with more up-time.
Proper Training and Our Training Opportunities
Operating water jet cutters is no easy task – especially when you add abrasives into the mix. Jet Edge offers a host of on-line resources, including blogs on best practice and maintenance videos to execute service. Our Technical Service Team is also there to help you with your water jetting needs and offers scheduled factory training classes. And if you need a little more Application Help, just let us know.
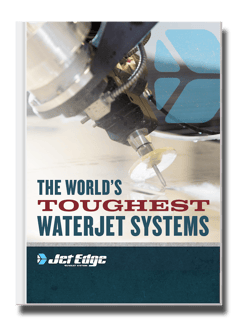
Check Out Our Digital Brochure!
Since 1984, Jet Edge has been designing and manufacturing Ultra-High-Pressure Water jet technology that doesn't back down. Our systems are used around the world in a broad range of industries from the world's leading airlines, to automotive, aerospace and industrial manufacturers, and machine job shops.
To learn more about the Jet Edge difference, our water jet motion systems, pumps and much more, click the button "Download Brochure" to get it now!