The most common methods for cutting sheet steel and plate steel includes Shearing, Laser Cutting, Plasma Cutting, Oxyacetylene Cutting and Waterjet Cutting. Each cutting method has advantages within its range of processing.
Common Cutting Methods at Metals Shops
Let's explore the variety of common cutting methods found in metal shops.
Shearing
Shearing is performed by a shear machine that produces straight line cuts only. They are generally used to blank sheets into smaller sizes quickly in preparation for other processes. The sheet thickness generally ranges from .005 – 0.25 inches, with a lower tolerance/accuracy.
Laser Cutting
“Laser” is an acronym that stands for Light Amplification by Simulated Emission of Radiation. The technology focuses high-intensity beams of light that can melt a cutline for thin metals that do not have reflective properties. With thin steel materials, lasers can be extraordinary fast and accurate with cuts. It utilizes heat, however, which creates a Heat Affected Zone and does not do advanced geometry cuts like bevels and contours. With a variety of wattage combinations available in the market, material thicknesses can range up to 1½ - 2 inches but may require a secondary operation for finish.
Plasma Cutting
Plasma metal cutting is considered the second most common method of cutting metal behind laser cutting. Like all other thermal cutting methods, Plasma Cutting is performed by melting metal. While plasma can cut thicker materials, in some instances mild steel up to 6 inches thick, it generates a larger Heat Affected Zone that makes the material harder and more brittle and creates a slight bevel in the cut face. Consequently, material thickness do not usually exceed 1 ½ - 2 inches thick. The 5,000 degree plasma arc creates warping on thinner materials and the top surface edge may be slightly better than the bottom edge. Plasma cut materials often require secondary operation to compensate for some of these deficiencies.
Abrasive Water Jet Cutting
Abrasive Waterjet Cutting delivers water that is under ultra-high pressure, usually 60k – 90k, to a cutting head where an abrasive mixture is introduced. It is a cold cutting process so there is no Heat Affected Zone and is the fastest growing precision cutting technology today. Abrasive Waterjet Cutting has grabbed the lead due to the range of materials that can be cut with great accuracy and high finish levels. All grades of steel, including Stainless, Titanium, Inconel and other Specialty Alloys can be cut using waterjet technology. Material thickness ranges from 6” on stainless steel to 20” inches on aluminum block. 5-axis cutting is available for complex geometric shapes and bevels cut to a very high accuracy and cut finish eliminating the need for secondary operations. With excellent sheet utilization, it is environmentally friendly with no harmful discharges.
Advantages of Cold Cutting with Water Jet Machines
Cutting with water jets offers several advantages over alternate methods, especially regarding stainless steel, Inconel, and other specialty alloys. However, the primary advantage is the significant reduction in heat during the cutting process. Using cutting methods that involve significant amounts of heat creates something called the HAZ (heat affected zone). This can damage materials around the cutting area – resulting is less efficient cuts, more machining required post cut, or worse – the scrapping of the material.
To learn more about using water jets to cut steel and other metals, check out some of these other blogs written about this topic:
- Cutting Titanium, Stainless Steel, and Other Specialty Alloys with Water Jet Machines
- Why Should I Use an Abrasive Water Jet Machine to Cut My Steel?
If You Need Help, Talk to an Expert
If you’re currently using alternative cutting methods that involve heat to cut your steel, talk to us at Jet Edge and see if a cold cutting process like water jet cutting is right for you. Our team of engineers is ready to help find the right machine for your product and/or material.
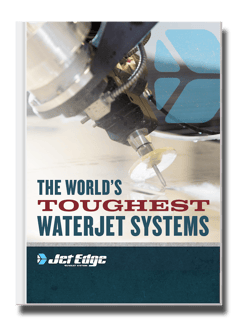
Check Out Our Digital Brochure!
Since 1984, Jet Edge has been designing and manufacturing Ultra-High-Pressure Water jet technology that doesn't back down. Our systems are used around the world in a broad range of industries from the world's leading airlines, to automotive, aerospace and industrial manufacturers, and machine job shops.
To learn more about the Jet Edge difference, our water jet motion systems, pumps and much more, click the button "Download Brochure" to get it now!